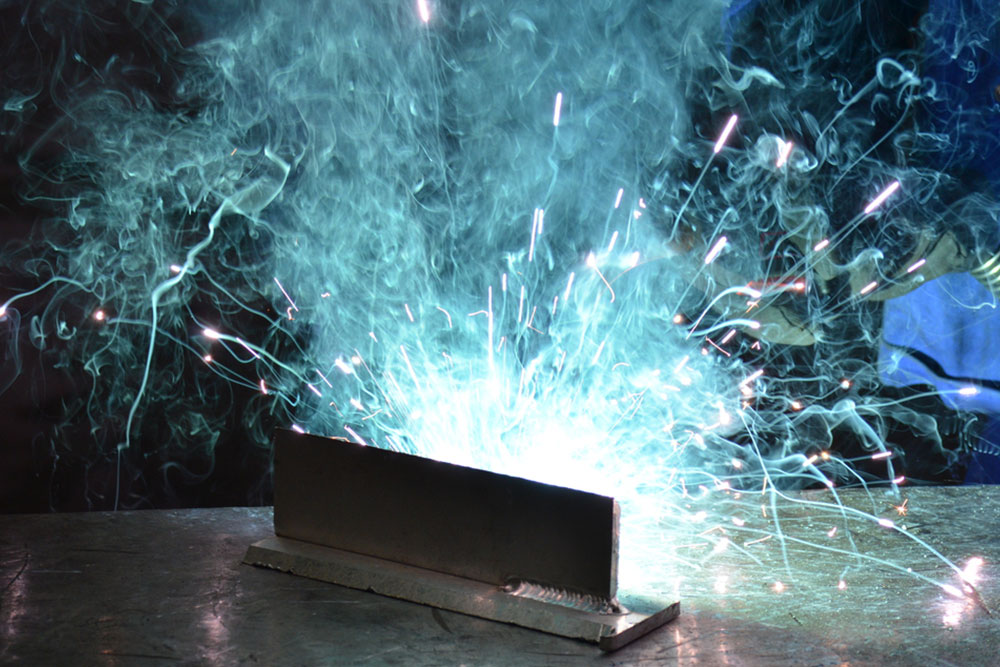
6 MIG Welding Tips For Perfect Results
MIG welding is considered beginner-friendly and is one of the best techniques for new welders who want to gain confidence and experience. However, while the process is relatively straightforward, the quality of your welds will depend on paying close attention to detail and taking into consideration some important factors. In this detailed guide, we outline the key MIG welding tips to help you achieve the best welds possible.
Choose the Right Equipment
Metal Inert Gas (MIG) welding is a technique that feeds a continuous wire electrode into a welding gun to create an electric arc between the wire and the metal being welded (base metal). This arc melts the two materials to form a weld while a shielding gas protects the weld pool from contamination.
Some of the equipment needed for this process includes:
- Welding gun
- Constant voltage power supply
- Wire feeder
- Shielding gas
- Electrode wire
- Ground clamp
Proper Setup
The first step is to prepare the welding area, cleaning both the base metal surface and the consumables. While the high temperature used in this technique can burn through contaminants, they can end up being trapped in the weld and this produces poor results. Cleaning facilitates proper fusion of the materials leading to strong welds.
Consumables include the nozzle, electrode wire contact tip, and gas diffusers. Every time you weld, they are likely to accumulate spatter, and cleaning them up before the next weld clears the buildup and unclogs the gas hole.
Another vital consideration is to attach the ground clamp to the welding table or workpiece before you begin. This will complete the circuit, keep the electrical arc stable, and provide proper electrical grounding. Good grounding should be as close as possible to the base metal and the surface should be clean and free of debris, paint, or rust.
Handle the Welding Gun Correctly
Firmly grip the welding gun using both hands for precise control and stability, particularly when welding long stretches or complex positions. Using both hands brings proper alignment and minimizes unintentional movements and accidental slips.
Maintain the correct angle (10 to 15 degrees) and depending on the material and your preference, use a push or pull motion to weld. Push motion is ideal when working with thinner materials as it produces a cleaner bead and fewer spatters. It is best for thicker materials as it is effective when working with higher heat and provides deeper penetration.
Maintain Proper Speed
Move the welding gun at a consistent speed to produce an even weld. Moving too fast is likely to limit penetration while going too slow can either lead to burn-through due to excessive heat or create an oversized bead. Maintaining the correct speed assists in even heat distribution, sufficient penetration for strong joints, and a clean weld.
Set the Right Stick-Out Length
Stick-out length refers to the distance between the contact tip of the welding gun and the end of the welding wire. The correct distance helps regulate the amount of heat applied to the weld, the stability of the arc, and the penetration.
If it is too short, the wire is likely to melt too close to the contact tip causing the wire to burn back. If it is too long, resistance will increase causing your current to drop. Additionally, it will result in less gas coverage and lower penetration, increasing the chances of spattering and creating a weak weld.
The ideal stick-out length should be between a quarter inch and half an inch, shorter for thinner materials and slightly longer for thick materials. Observe the arc during welding and if you notice instability, lack of penetration, or spatter, adjust the length accordingly.
Dealing with Different Materials
Different metal types and thicknesses call for variations in the technique used, shielding gas, electrode wire type, and machine settings. Thicker materials require a higher voltage and faster wire feed for proper penetration, while thinner materials need greater control and lower speeds to mitigate the risk of burn-through. Choose the right gas or gas combinations for different metals.
Improve the Quality of Your Welding Projects with Professional Services
Are you a hobbyist or an aspiring professional welder? Taking into consideration the above MIG welding tips will help you improve the quality and appearance of your welds.
The best way to master the technique is by experimenting with subtle changes in the travel angle, speed, and voltage and monitoring how these changes affect the results. With practice and keen attention to detail, you will develop the skills needed to produce clean, strong welds.
As you continue to refine your technique, having a deep understanding of the process will go a long way in helping you achieve the desired results. Our team of metal fabricators at Gauer Metal Products, Inc. has honed its expertise in MIG, TIG, and spot welding services over the past 78 years.
We have carved out a niche for offering unmatched metal fabrication solutions. We design, engineer, and manufacture top-quality products using all types of metals, and have what it takes to deliver exceptional results. No matter how complex your project is or how unique your needs are, we guarantee top-tier results for all your requirements.