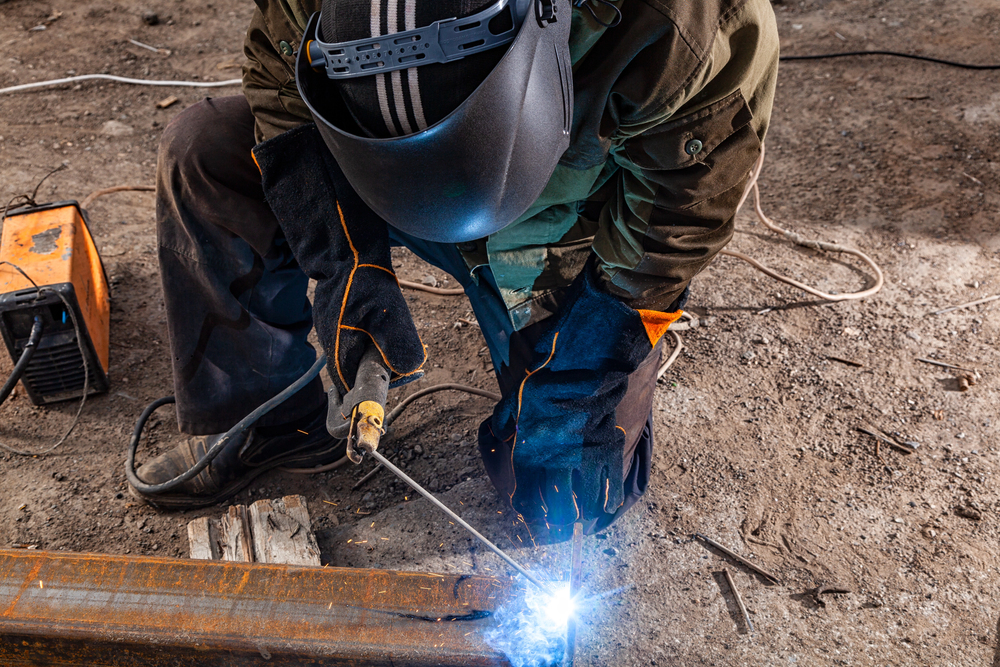
What Is MIG Welding And How Does It Work?
MIG welding is one of the most popular welding processes that fabricators and manufacturers use to join metals together. It is highly reputed for its versatility and ease of use and is widely used across diverse industries. In this guide, we will answer the question “What is MIG welding?”, and find out how it works and how it compares to other popular welding techniques.
What is MIG Welding?
Metal inert gas (MIG) welding is also known as wire welding or short-circuit welding. It is a type of gas metal arc welding (GMAW) that uses a consumable wire as the filler material as well as the electrode.
How It Works
MIG welding uses three main materials:
- A welding gun
- Filler metal
- An inert gas (such as argon)
The process involves feeding a continuous consumable wire electrode and an inert gas to a welding gun simultaneously. When a fabricator pulls the trigger on the welding gun, it draws on a constant electric voltage to produce a large amount of heat (over 5,400 degrees Fahrenheit), creating an electric arc. The arc melts both the filler metal and the workpiece or base metal, fusing them together.
The role of the inert gas (shielding gas) is to create a protective shield around the weld pool in the form of an inert atmosphere. It therefore keeps the material from reacting with oxygen or moisture in the air and getting contaminated, which could weaken it or lead to rusting due to the presence of impurities.
One of the most important considerations in this process is keeping the voltage constant so as to keep the arc steady and predictable during welding. The power source used has to maintain a steady output even as the current fluctuates based on the speed of the electrode feed and the arc length.
If the electrode wire gets too close to the workpiece, shortening the arc length, the current increases rapidly burning off the extra wire and restoring the arc length to the desired level. Similarly, if there is an increase in arc length, the current reduces allowing the wire to build up and restore the arc length to normal.
Regardless of changes in welding conditions, a steady power supply keeps the voltage constant. This makes sure of consistency in the weld, keeps it clean, and calls for less manual intervention.
A Brief History of MIG Welding
MIG welding traces its history back to 1948 when it was first used in the USA as an invention of the Air Reduction Company. It was the first process of its kind to use a single piece of metal as both the electrode and the filler material.
Prior to the invention of MIG welding, fabricators and manufacturers would typically use stick electrodes, also known as Shielded Metal Arc Welding (SMAW) electrodes. This consumable electrode which was used to create the electric arc was coated in flux. The flux coating would melt during welding to protect the weld pool from contamination. The main downside of this approach was the speed at which the stick electrodes would deteriorate during the welding process.
In light of this, MIG welding presented a welcome innovation as it involved feeding a wire electrode continuously through the machine, thus eliminating tedious interruptions. Furthermore, since the process did not use any flux, it would produce a clean weld and would not require slag removal as was the case with traditional methods.
It was a much faster and cleaner method of welding, and a game-changer for industries whose production processes involved metal fabrication. At the onset, this method was primarily used in welding non-ferrous metals such as aluminum. However, with time, it evolved to include additional materials such as steel.
Back then, it was expensive, required complex welding materials and had a steep learning curve. Meanwhile, its benefits outweighed the cons and as demand increased, the process evolved with notable improvements in technique and equipment.
MIG Welding Today
Thanks to its numerous advantages, MIG welding remains one of the most popular welding methods today. Technological improvements have aided the creation of compact and user-friendly machines that make the process a lot more accessible. Consider some of its benefits:
- Easy to learn and use
- Cost-effective
- Can work with a variety of materials
- Offers fast welding capabilities
- Clean welds
Compatible Materials
Steel
The main challenge fabricators face when welding steel is how to achieve a strong weld without using too much heat, as this would damage the surrounding material or cause warping. Steel is also known for its high strength, and variable thickness.
MIG welding comes with excellent penetration in both thick and thin steel sections. It uses a constant voltage and controlled heat supply, minimizing the possibility of overheating or distortion, and allowing for better control.
Stainless steel
At high temperatures, stainless steel is prone to oxidation, which can compromise its corrosion resistance and weaken the weld. It also has high thermal expansion and exposure to high heat can cause distortion. Because this process uses controlled heat and a shielding gas, it overcomes these issues, preventing contamination and distortion, and retaining the material’s corrosion resistance.
Aluminum
As a highly conductive metal, aluminum dissipates heat extremely fast. When using alternative welding methods, this makes it challenging to maintain a stable arc and achieve proper penetration. Additionally, the metal forms a natural oxide layer that can contaminate the weld. MIG welding delivers controlled heat for proper fusion and minimal spatter.
Nickel Alloys
Nickel alloys are challenging to weld due to their heat resistance, high strength, and the possibility of cracking or becoming porous at high temperatures. For nickel alloys, MIG welding is the ideal choice because it provides the high heat input they require, particularly for thicker sections.
Copper
Copper is challenging to weld because it requires very high heat to melt. Moreover, its high conductivity means it absorbs and transfers heat rapidly, which can result in rapid cooling during welding. When this happens, it can form a brittle joint or result in heat deformity.
MIG welding is a suitable choice because it uses a very high temperature and brings efficient heat control.
MIG Welding vs. TIG Welding vs. Spot Welding
Without question MIG and TIG welding are among the most common welding processes used today. Here are some key differences between the two:
- Process
MIG welding uses a continuous wire electrode to create an arc that melts both the wire and base metal, creating a weld pool that fuses the metals together.
TIG welding uses a non-consumable tungsten tip as an electrode to join metal surfaces by heating them together. The sole purpose of the tungsten tip is to maintain the arc. The electrode melts the base metal and the fabricator manually adds a filler rod to the weld pool as needed.
Spot welding is a type of resistance welding used to join two sheets of metal together by applying heat and pressure at specific points or spots.
- Materials
While MIG welding is preferred for thicker materials and works well with a variety of metals, TIG welding is suitable for thinner materials and works best with titanium, exotic alloys, stainless steel, and aluminum. Spot welding is typically used to join thin sheet metals, mostly aluminum, stainless steel, and mild steel.
- Precision
MIG welding is good for structural welds while TIG welding offers high precision and is ideal for the fine welds typically required in the medical, art or aerospace fields. Though spot welding produces clean welds, it is localized to small spots.
- Cost
MIG welding is more cost-effective as it has a lower learning curve and gives faster welding speeds. Comparatively, TIG welding has a relatively steep learning curve, is more labor-intensive, and comes with slower welding speeds. Spot welding machines are costly but material costs are low since it does not require filler material.
Why Choose Gauer Metal Products, Inc. for Your Welding Needs
Gauer Metal Products, Inc. has been providing metal fabrication services for the past 78 years. During that time, we have been part of the incredible revolution that has transformed the industry as a whole, and welding processes in particular.
We are skilled in delivering excellent MIG, TIG, and spot welding services, adapting our approach to the materials in use and the requirements of the project. No matter what you have in mind, we have the expertise and experience to bring the most ideal custom metal fabrication solutions for your project. Contact us today.