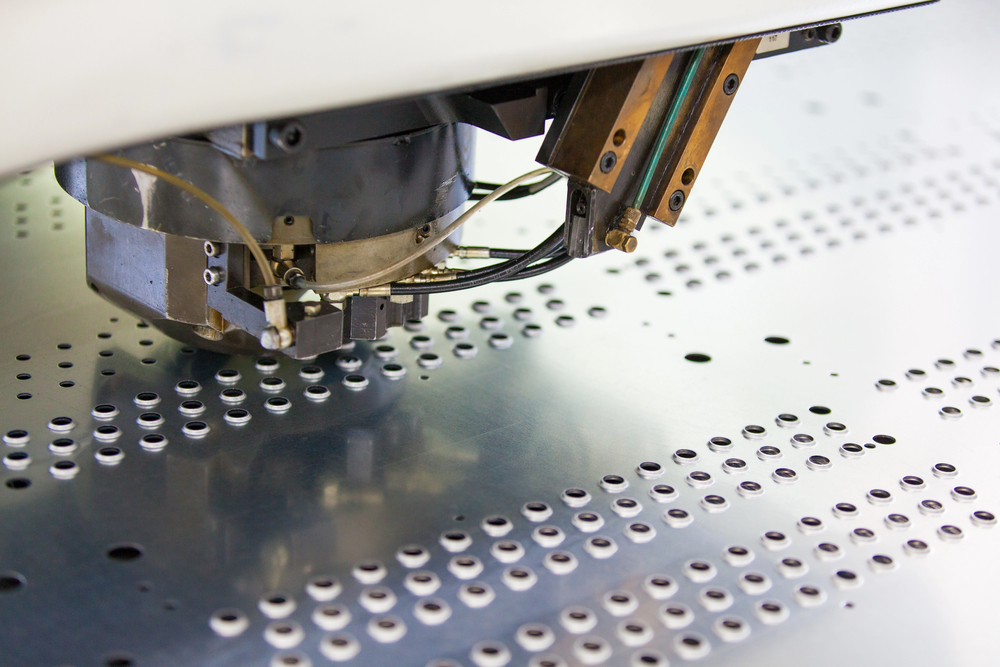
All You Need To Know About The Metal Punching Process
The metal punching process is a core component of modern manufacturing, playing a significant role in shaping materials into precise designs. With its ability to handle a wide range of metals, this method has revolutionized industries by offering efficiency, versatility, and accuracy. Knowing the mechanics, applications, and benefits of this technique is important for businesses seeking reliable fabrication solutions.
What Is Metal Punching?
It is a manufacturing process where a punch press uses force to create holes or shapes in sheet metal. This process is achieved by driving a punch through the material into a die, which holds the desired shape. It is widely used in industries such as automotive, electronics, and construction to produce components that require precision.
The process is highly adaptable and capable of working with various metals including aluminum, steel, and copper. Whether creating simple holes or intricate patterns, the process can accommodate complex specifications while maintaining consistent quality.
How the Metal Punching Process Works
The process relies on three primary components: the punch, the die, and the press. The punch acts as the tool that applies pressure, while the die determines the final shape. Together, they work in tandem to remove unwanted material from the sheet. This leaves a clean and accurate design.
It begins with a flat sheet of metal placed on the press bed. Using mechanical or hydraulic force, the punch is driven into the material, cutting out shapes or perforations. Modern techniques, such as CNC (Computer Numerical Control) punching, allow for automated and highly precise operations. They significantly enhance production speed.
Benefits of Metal Punching
One of its key advantages is efficiency, especially in high-volume production. The process is cost-effective, as it minimizes waste by reusing scrap material whenever possible. This feature is particularly advantageous for industries that require large-scale production without compromising quality.
In addition to efficiency, the process brings exceptional precision, thereby, enabling manufacturers to produce consistent designs across multiple units. The process is also versatile, accommodating different metal types and thicknesses. Whether for industrial equipment or custom metal fabrication, this method adapts to diverse needs with ease.
The Role of Metal Punching in Custom Metal Fabrication
This process has a great role in custom metal fabrication by enabling the creation of unique designs and intricate patterns. It allows manufacturers to cater to specific project requirements. Therefore, it produces components that meet exact dimensions and tolerances. Custom fabrication often requires precision and versatility, both of which are core strengths of metal punching.
In addition to creating one-of-a-kind parts, this method supports rapid prototyping and small-batch production. Its adaptability makes it an ideal choice for businesses looking to innovate and experiment with designs. Manufacturers can achieve a balance between creativity and efficiency by incorporating this technique into their workflows.
Applications of Metal Punching
Its applications extend across various industries due to its reliability and adaptability. In the automotive sector, it is used to manufacture components like brackets, panels, and structural supports. Similarly, in the electronics industry, this process plays a vital role in creating housings, connectors, and circuit boards.
Construction projects also benefit from this method, as it facilitates the production of structural elements, fittings, and decorative features. Beyond these industries, manufacturers of household appliances and industrial machinery rely on this technique to achieve precise, durable parts. Its versatility makes it a preferred choice for businesses seeking innovative fabrication solutions.
Types of Machines Used in Metal Punching
Machines made for the process come in different forms, each suited to specific production requirements. Manual punch presses are ideal for small-scale operations, offering simplicity and control. Hydraulic presses, on the other hand, provide greater power. They are suitable for thicker materials and larger production runs.
CNC punching machines represent the most advanced option, combining automation with exceptional accuracy. These machines use computer programming to control the punch and die. They allow for complex and customizable designs. The choice of machine often depends on the project’s scale, complexity, and material specifications.
Factors to Consider in Metal Punching
Several factors influence the success of the process, including material type, thickness, and design complexity. The material must be strong enough to withstand the punching force without warping or cracking. Similarly, the thickness of the sheet determines the required press strength helping so that it achieves optimal results without damaging the equipment.
Design specifications also play a significant role, as intricate patterns may require advanced tools or CNC capabilities. Addressing these factors can help optimize their processes and achieve high-quality outcomes. Partnering with experienced professionals further enhances the reliability of the final product.
Advancements in Metal Punching Technology
The process has evolved significantly with advancements in technology. CNC punching machines now dominate the industry. These systems allow for quick adjustments, reduced production time, and the ability to handle complex designs with minimal human intervention.
Moreover, modern machines are equipped with sensors and software that monitor performance and detect errors in real-time. This innovation improves overall accuracy and reduces material waste. The integration of digital tools into this process demonstrates the industry’s commitment to meeting the demands of modern manufacturing.
Metal Punching and Sustainability
As sustainability becomes increasingly important, this particular process also contributes to eco-friendly manufacturing practices. It generates minimal waste, as scrap material can be recycled or repurposed. This efficiency aligns with industry efforts to reduce environmental impact while maintaining cost-effective production.
Furthermore, advancements in machinery and automation help conserve energy during operations. Sustainable practices do not only benefit manufacturers; they also support broader environmental goals. This focus on sustainability reinforces its value in the modern fabrication landscape.
The Future of Metal Punching
Its continued technological innovation and adaptation to new manufacturing needs dictate the role it plays in the future. Developments in automation, robotics, and artificial intelligence are expected to enhance efficiency and precision further. These advancements will enable manufacturers to tackle increasingly complex projects with greater ease.
In addition, the demand for lightweight and durable materials will shape the evolution of punching techniques. As industries prioritize customization and sustainability, the process will remain a cornerstone of fabrication, providing innovative solutions to emerging challenges.
Challenges in the Metal Punching Process
While it is a highly efficient and reliable manufacturing technique, it does come with its own set of challenges. These include tool wear, material deformation, and achieving consistent precision in complex designs. Over time, frequent use of the punch and die can lead to wear, affecting the quality of the final product. Regular maintenance and proper material selection are required in order to mitigate these issues.
Another challenge is dealing with thicker or harder metals, which may require specialized equipment or adjustments to the punching process. Manufacturers must also account for potential burrs or rough edges, which may necessitate additional finishing steps.
Comparing Metal Punching to Alternative Methods
The process remains a popular choice, and while that is the case, it is often compared to alternative fabrication methods such as laser cutting and stamping. Laser cutting, for instance, excels at producing highly detailed designs with smooth edges. However, it is generally more expensive and slower than metal punching for high-volume production.
Stamping, on the other hand, shares similarities with punching but is typically used for creating multiple identical parts in a single operation. Unlike stamping, punching offers greater flexibility for projects requiring varied designs or adjustments. Knowing these differences helps manufacturers choose the most suitable process for their specific needs depending on a series of diverse applications.
Expert Solutions for Your Fabrication Needs
If you are looking for expert punching and stamping services, Gauer Metal Products, Inc. is here to help. With decades of experience and cutting-edge technology, we deliver high-quality results tailored to your specifications. Contact us today to learn more about our capabilities and how we can bring your designs to life.