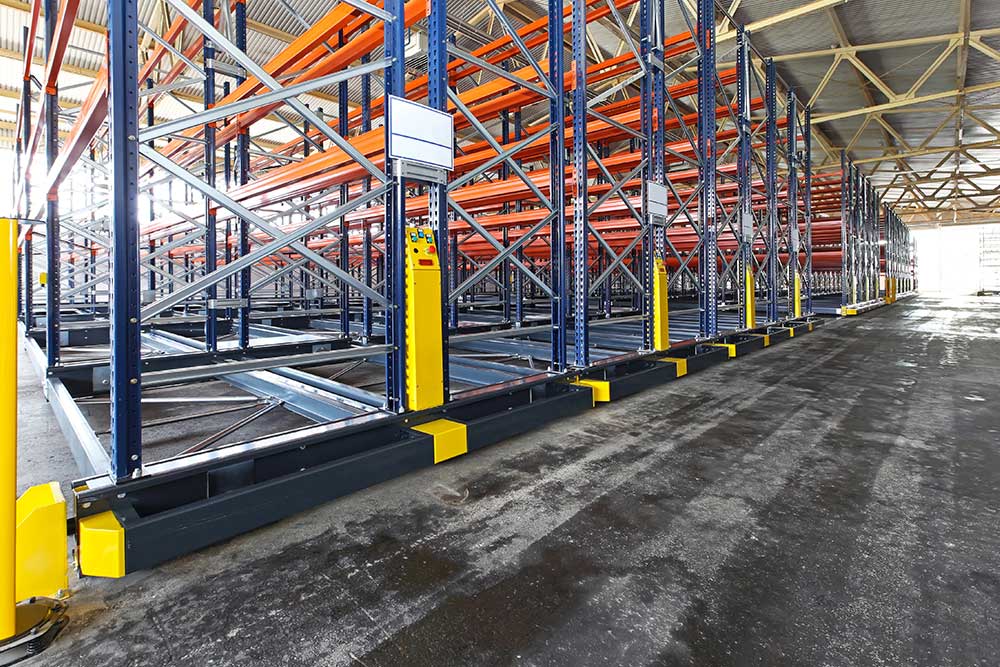
How To Select The Best Warehouse Racking System For Your Business
Choosing the right racking system in your warehouse can be quite the game changer, as it can better optimize your whole operation for a smoother and more efficient setup. A well-designed system not only ensures sufficient space but also promotes proper inventory management, and space utilization. The right racking in a warehouse is not only necessary for inventory storage but also contributes to being a more productive and safe work environment. An understanding of your particular business demands as well as an analysis of the many racking system elements will guide you to an informed choice. The following guide provides step by step instructions to choose the most suitable racking system for your warehouse requirements.
Assess Your Warehouse Needs
Review the assortment of products, their quantity, and the arrival frequency of goods and the timeframe of their delivery. This is the information you will need to select the appropriate racking system for your warehouse. Look at the operational sequence and make sure the racking system really allows for the least possible disruptions and maximum workflow efficiency. By carefully evaluating your requirements you can select a racking system that not only increases productivity but also organizes the whole warehouse.
Don’t forget to consider the potential growth of your operations when evaluating your racking needs. As your business grows, your requirements for storage may also increase. Opting for a racking system that can be adjusted to meet these demands will save you time and money. Discuss with your management team to have a clear picture of all potential scenarios. This will let you determine if the racking system you choose will be able to accommodate your current operations as well as your future needs.
Determine Product Dimensions and Weight
Knowing rough dimensions and weight of the inventory is necessary for a proper racking system. Heavy or bulky items may need a more durable and special racking solution. Proper measurements will prevent proper storage of goods and ensure the safety of your warehouse workers. Log the size and weight of each product type and use this data to choose your racking solutions.
The kind of materials you are storing is also one of the factors to consider. For instance, delicate items require extra padding or support. Make sure that the racking system you are using can support the weight and size of the products with added padding or support. An ideal racking system is one that will not only lower the risk of accidental damage but also extend the life of your products and the racking system itself.
Consider Inventory Turnover Rate
Your inventory turnaround rate has a major impact on the choice of the racking system. Fast-moving products require quick retrieval and processing, therefore, selective pallet racking systems are preferable for such operations. In contrast, slower-moving inventory can be stored in deeper, more compact racking systems to save space. Your turnaround rate analysis will help you choose a system that improves productivity and optimizes processing time.
Knowing the seasonal variations in your inventory turnaround rate is equally important. At times of peak demand, there may be a higher access frequency, thus your racking system should be designed to accommodate such changes from time to time. A well-constructed racking system that is in line with your turnaround rate will not only enhance operational efficiency but also help lower handling labor. This systematic approach will ensure your warehouse run smoothly all year long.
Evaluate Available Warehouse Space
Measuring the space in your warehouse is an easy yet crucial step for determining a suitable racking system. Look at the floor space, measure the height of the ceiling, and check for any possible obstacles that can affect the installation of the rack. You can determine where to set up the racking system and what layout best suits your operational needs.
Check that the racking system provides a safe passageway for workers and forklifts to move freely. Optimal distances between racks will ensure the smooth retrieval of inventory and ensure the spaces are free of congestion to minimize workplace injury. Analyzing the warehouse layout in detail will help you put together a storage space that is not only efficient but also offers ease of movement.
Calculate Your Budget
Decide on the amount you are going to invest in the racking system and think of the benefits that will come from it. Despite the fact that there are cheaper options, investing in a quality racking system will benefit you in the long run due to less probability of breakdowns and prolonging the efficiency of your operations.
Considering overall ownership costs would need to include expenses for the installation, service, and improvements. A well-organized racking system that is cost-effective while matching your needs will be a solution that would bring profits. Don’t forget to set aside a part of your budget meant for any future modifications and expansions, so the racking system would still be effective as your business continues to grow.
Prioritize Safety and Compliance
Racking system design must be done with safety and compliance. Make sure that the system is in accordance with industry and safety standards. The weight, motions, and reinforcement accessories like guardrails and safety nets are the aspects that should be taken into account.
Having your employees participate in the safety training can also help to avoid any accidents and injuries at the workplace. It is necessary to train all the workers using or working around the racking system to adhere to the safety guidelines.
Explore Different Racking Systems
There are several types of racking systems, with each one delivering unique capabilities. The most popular selective racking system allows access to any pallet at any particular time. Drive-in racking on the other hand, takes up lesser space in the aisle to make room for more pallets. The push-back racking system is the most ideal for those seeking a systematic process while maximizing inventory density. Pallet flow racking is popular due to its FIFO storage method. Each system has their own particular characteristics and consequently, the right system is one that suits your unique storage needs.
Drive-in racks are suitable for large volumes of similar products. Selective racking, in contrast, gives you quick access to a variety of goods. Push-back racking is for medium turnaround items while pallet flow racking is the best choice for high turnaround products. When picking a racking system, consider the type of inventory you have and how frequently it needs to be accessed.
Consider Racking System Capacity
Evaluation of the racking system capacity is a must so as to ensure the system can handle the storage requirements of your warehouse. The racking system must be able to withstand the dimension and weight of your inventory as well as maintain the safety of the workers and other facilities. Safety hazards and interruptions of operations due to overloaded systems are some of the reasons why it is crucial to ensure the system has sufficient capacity to accommodate your storage requirements.
Overall racking system capacity can also be estimated by determining the layout of your warehouse. Use this tip to be sure of the physical floor space, the material and size of pallets, as well as the type and weight of the products you intend to store. Ensure the racking system is not only flexible enough to adapt to future changes in your operations but also to accommodate any amendments in layout.
Evaluate Accessibility and Pick Efficiency
The time workers take to pick inventory will determine the efficiency of your warehouse operation. Systems such as selective racking can be more efficient in order fulfillment due to the easy access of each pallet. Drive-in racking, on the other hand, is a high-density system that has restricted accessibility but is highly efficient in terms of inventory loading. Reflect on the frequency of inventory access that you will need and select a racking system that will offer both storage density and accessibility.
Think About Future Growth
Your preferred system should be able to be upgraded or adjusted easily if there are any modifications in inventory type and weight or warehouse configuration. The system’s flexibility will be able to keep up with your storage needs as your business grows. Having a plan in place for when the operations expand both in quantity and in diversity will save you from the trouble of expensive replacements.
Future growth is not only about adding new products but also about changing your business model. The flexibility of your racking system lets you reconfigure easily to match new storage needs. Spending on a scalable plan now will make your work easier in the future and help you maintain sustainability as the system will continue functioning as it should for an extended period of time.
Consult with a Racking Expert
When consulting a racking expert, take note of different points of view on the different concerns you may have on selecting the best racking system for you. Professionals can analyze your warehouse layout, inventory type, and operational requirements to suggest the racking solution that is most appropriate for you.
Racking experts can also suggest options that are most suitable for your warehouse layout and your storage needs. A session with a professional can smoothen the whole process and make you feel assured that you are indeed choosing the right racking system.
Measure ROI of Racking System
Measuring the return on investment (ROI) of a racking system is key in gaining an insight into the system’s contribution to the success of a business. Calculate the cost savings achieved through improved storage efficiency, picking times, and better space utilization. Include these savings along with the original investment to calculate the overall functionality of the system. High ROI is a sign of a successful investment which, in turn, is a positive contributor to the growth of your business.
Measuring the ROI also includes monitoring the changes in operational efficiency and productivity over time. Keep track of the main performance indicators like order fulfillment times, inventory accuracy, and space utilization before and after installing the racking system. The data shows the advantages of the system and proves that the investment can be justified in the long run.
Check Racking System Warranty
A warranty demonstrates the manufacturer’s assurance that the product quality and durability are guaranteed. Weigh the warranty terms beforehand to know what is included and for how long. The advantages of getting an extensive warranty include gaining peace of mind and protection from possible defects or problems that may arise down the road. The warranty should also include different aspects of the racking system like materials, workmanship and structural integrity. Check whether the warranty is complete and gives you the required peace of mind for your investment.
Optimize Your Storage with Carton Flow Rack Systems from Gauer Metal Products
Ready to boost your warehouse operational efficiency? Our Gauer Metal Products Flo-Rak carton flow rack system is the perfect solution for you. It provides a very efficient means of storage and access for smooth inventory management and order fulfillment. In addition to our racking systems, we offer custom-made sheet metal fabrication services that are durable and completely customizable to meet your unique needs. By partnering with us, you are guaranteed high-quality, made-in-the-USA racking solutions that are designed to meet your operational needs and support future growth. Connect with our team now to find out how we can change your storage systems and increase your operational productivity.