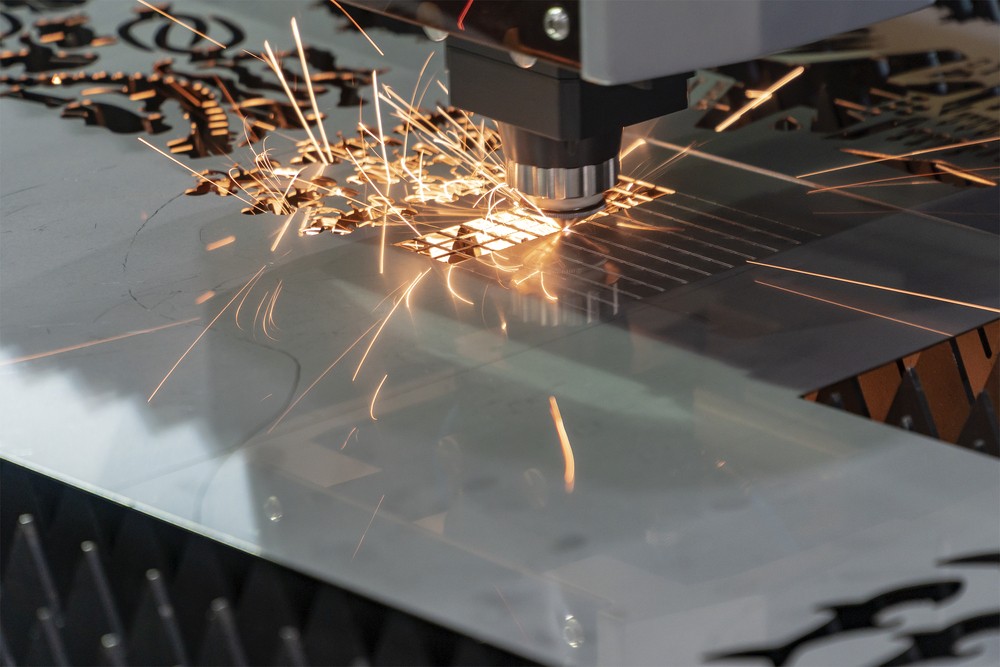
Sheet Metal Fabrication Demystified: What You Need To Know
In the world of manufacturing, precision and quality dictate success. Sheet metal fabrication is a pivotal process in the production of metal parts and assemblies in industrial manufacturing. Its applications are vast, ranging from automotive components to intricate electronics and robust architectural elements.
In our comprehensive article, we will take a look at the ins and outs of this process to understand how it works and what makes it a preferred choice for high-quality metal products.
What Is Sheet Metal Fabrication?
Sheet metal fabrication is a manufacturing process that involves converting sheet metal into equipment parts and products.
This technique is used across industries to produce components for machinery, vehicles, appliances, and buildings. It involves specialized procedures like stamping, folding, and welding, for the creation of durable and precise metal products tailored to specific design requirements.
Let us take a closer look at what it entails.
The Core Processes
● Cutting
One of the primary steps in this fabrication process is cutting the metal into the required shapes. Modern techniques have evolved far beyond manual shears and saws. Today, precision cutting technologies such as laser cutting, water-jet cutting, and plasma cutting allow for clean, sharp edges and complex contours.
These methods ensure accuracy and reduce waste, making the process more efficient and environmentally friendly.
● Bending
The second step involves bending the metal into specific angles using press brakes, folding machines, or even by hand in smaller workshops. The choice of bending technique largely depends on the project requirements, the type of metal being used, and the desired precision. Techniques like CNC bending provide unmatched accuracy, which is crucial for the assembly of complex structures.
● Assembling
After cutting and bending the components, the next step is to assemble them into final products. This can involve various techniques such as welding, riveting, threaded fasteners, or adhesives.
The choice of assembly method impacts not only the aesthetics of the final product but also its durability and performance under different conditions.
Materials Used in Fabrication
The choice of material significantly affects the outcome of the fabrication process. Common materials include:
- Steel: Known for its durability and strength, steel is a popular choice for both structural and functional parts.
- Aluminum: Lighter than steel but equally robust, aluminum is favored for applications where weight is a concern, such as in the automotive and aerospace industries.
- Copper: Highly conductive and corrosion-resistant, copper is ideal for electrical components and decorative elements.
- Brass: A mixture of copper and zinc, brass is used for its acoustic properties in musical instruments and its resistance to corrosion in marine environments.
Each material requires specific handling and processing techniques to maximize its properties and ensure the final product meets quality standards.
Expanding Material Horizons
The exploration of new materials and composites plays a significant role in the evolution of metal fabrication. Innovations in material science, such as the development of ultra-high-strength steel and lightweight aluminum-magnesium alloys, offer new possibilities for durability and efficiency in fabricated products.
These materials can provide enhanced properties like increased corrosion resistance, better thermal conductivity, and greater strength-to-weight ratios. As the industry continues to test and integrate these advanced materials, the potential for creating more innovative and efficient products grows, opening up new markets and applications.
Innovations in Fabrication Techniques
The field of metal fabrication has seen significant technological advancements that have streamlined processes and improved outcomes. Automation and robotics have been game-changers, allowing for more precise cuts, consistent bending, and faster production times.
Additionally, software advancements, particularly in computer-aided design (CAD) and computer-aided manufacturing (CAM), have revolutionized how projects are conceptualized and executed.
These tools enable designers and fabricators to create detailed models and simulations before the physical manufacturing begins, reducing the risk of errors and material waste.
Applications in Various Industries
The versatility of sheet metal fabrication makes it indispensable across multiple industries. In the automotive sector, it is used to create everything from chassis components to intricate engine parts. In construction, it provides essential elements such as beams, roofing, and decorative facades.
The electronics industry relies on precisely fabricated metal parts to house and protect sensitive components, while consumer products from appliances to furniture often incorporate metal parts produced through this method.
Quality Control in Sheet Metal Fabrication
Quality control is paramount in sheet metal fabrication to ensure that every component meets stringent standards before being used in further manufacturing or sold as a final product. This part of fabrication focuses on maintaining precision, adherence to specifications, and ensuring the durability and functionality of the metal parts.
Implementing Standards and Certifications
To achieve high levels of quality, fabricators adhere to a variety of standards and certifications. These may include ISO (International Organization for Standardization) certifications, which guide manufacturing processes to meet international standards for quality and safety.
For industries requiring even more rigorous controls, such as aerospace or medical device manufacturing, additional certifications like AS9100 and ISO 13485 are common.
Inspection Techniques
Modern metal fabrication shops employ advanced inspection techniques to ensure that each part is produced correctly. These methods include:
- Visual Inspection: The simplest form of inspection involves a detailed examination of the part by experienced personnel to identify any visible defects.
- Dimensional Measurement: Tools such as calipers, micrometers, and coordinate measuring machines (CMM) are used to measure the physical dimensions of a part and verify that they match the design specifications.
- Material Testing: To ensure that the materials used can withstand the conditions they will be subjected to, tests such as tensile strength, hardness, and corrosion resistance are conducted.
Continuous Improvement
Continuous improvement processes are integral to maintaining quality in fabrication. Manufacturers often use a variety of techniques to help in identifying inefficiencies and reducing waste, while also improving the overall quality of the output. These methodologies focus on data-driven decision-making and are pivotal in achieving operational excellence.
Cost Management in Sheet Metal Fabrication
Efficient management of costs is crucial for maintaining competitiveness in the metal fabrication industry. Several factors influence the cost-effectiveness of the fabrication process, and understanding these can help in making strategic decisions that affect the bottom line.
Material Selection
The choice of material not only affects the properties of the final product but also the cost. For example, using aluminum might be more expensive than steel, but it could reduce costs in industries where lighter weight is beneficial, such as in aerospace or automotive applications.
Production Techniques
The selection of cutting, bending, and assembling techniques directly impacts production costs. Advanced techniques like laser cutting are often more expensive upfront. However, they may reduce the need for secondary finishing processes and decrease waste material, thereby saving costs in the long run.
Economies of Scale
Volume production can significantly reduce the cost per unit. By increasing order sizes, fabricators can optimize their resource utilization and distribute fixed costs more effectively across a larger number of parts. Negotiating supply contracts and improving production scheduling are key strategies used to capitalize on economies of scale.
Sustainability and Environmental Impact
Sustainability has become a critical consideration in all manufacturing processes, including sheet metal fabrication. Implementing environmentally friendly practices not only helps protect the environment but can also improve the company’s public image and compliance with regulatory requirements.
Reducing Waste
Waste reduction is achieved through efficient layout planning, nesting software that optimizes material usage, and recycling scrap metal. These practices help in minimizing environmental impact while also reducing costs associated with material purchases.
Energy Efficiency
The metal fabrication industry is energy-intensive, especially processes like melting and creating formed shapes. Adopting energy-efficient technologies and practices, such as using newer, more efficient machinery or optimizing the production process to minimize energy consumption, is crucial.
Use of Sustainable Materials
Where possible, using recycled materials can significantly reduce the environmental footprint of fabrication processes. Many metals, including steel and aluminum, can be recycled without degradation in quality, making them ideal for sustainable manufacturing.
Safety in Metal Fabrication
Safety is a paramount concern in the metal fabrication industry, given the use of heavy machinery, sharp materials, and high temperatures. Complying with regulatory requirements is an essential part of upholding safety measures. Another important aspect involves the adoption of advanced safety technologies and training.
Modern fabrication shops are increasingly utilizing automated safety sensors and machine guards that prevent accidents. Additionally, ongoing training programs are essential to educate workers about new safety protocols and equipment.
By prioritizing safety, companies protect their employees and improve productivity, as fewer accidents mean less downtime and lower costs related to injuries.
Future Trends and Innovations in Metal Fabrication
The metal fabrication industry is continuously evolving, driven by advancements in technology and changing market demands. Staying ahead of these trends is crucial for companies to remain competitive and innovative.
Let us explore the emerging technologies and methodologies that are shaping the future of metal fabrication.
Integration of Advanced Technologies
The adoption of advanced technologies such as 3D printing and artificial intelligence (AI) is revolutionizing the metal fabrication industry. 3D printing, also known as additive manufacturing, allows for the creation of complex, lightweight structures that would be difficult or impossible to achieve with traditional methods.
AI and machine learning are being used to optimize production processes, predict maintenance needs, and enhance quality control, leading to higher productivity and reduced costs.
Increased Automation
Automation in metal fabrication is not just about robotics. It extends to fully automated production lines that integrate fabrication processes. These systems improve precision and speed while reducing labor costs and human error.
As automation technology becomes more sophisticated and affordable, its adoption is expected to increase, even in smaller fabrication shops.
Focus on Customization
As markets move towards more personalized products, the ability to customize metal parts quickly and economically is becoming a competitive advantage. Advanced software and flexible manufacturing systems allow for rapid changes in production runs to accommodate custom orders without significant downtime or cost increases.
Gauer Metal Products Is at the Forefront of Metal Fabrication
For over seven decades now, Gauer Metal Products has been at the forefront of metal fabrication trends. Our expertise in design, engineering, and manufacturing allows us to adapt quickly to new technologies and market demands.
We offer customized sheet metal fabrication services for all metals to meet your specific needs. Whatever your needs are, we have the expertise to deliver high-quality solutions tailored to your specifications. Our processes make use of advanced technologies and tools to optimize fabrication capabilities.
For instance, our Hydraulic and Mechanical Safety Edgers help in the production of high-quality edged flat bars and other flat bar products. With these tools on hand, we produce high-precision and complex metal parts efficiently, maintaining the highest standards of quality at a low cost. Choose Gauer Metal Products and let us guide you through every step of your metal fabrication project from conception to completion.