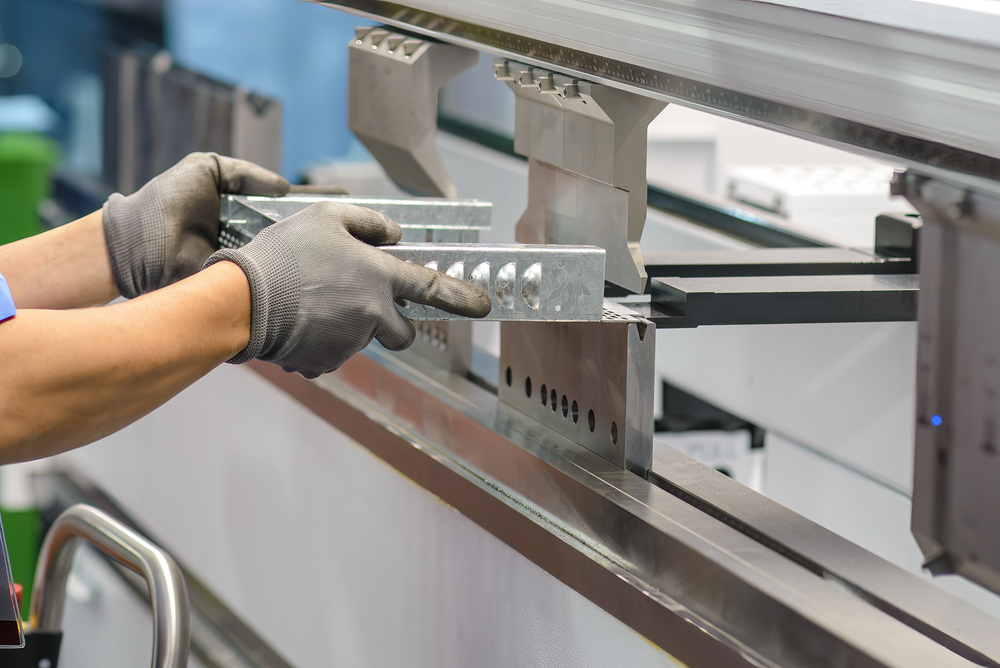
Understanding Sheet Metal Bending Calculations
In industries that require tight tolerances, the slightest inaccuracies in sheet metal bending can cause component failure or malfunctions. The ability to obtain consistently accurate bends revolves around meticulous sheet metal bending calculation.
Our team of experts at Gauer Metal Products, Inc. is highly skilled and experienced in metal bending and forming services. We understand the numerous benefits that come with sheet metal bending in fabrication. Thanks to our meticulous attention to detail, advanced machinery, and refined craftsmanship, we have the capacity and capability to meet your project needs.
Behind each of our flawless bends and high-quality products is a careful calculation of various metrics. Let us find out how getting these calculations right helps us turn metal sheets into top-notch components for your applications.
What is Sheet Metal Bending?
Sheet metal bending is the manufacturing process that deforms flat metal sheets into a specific shape without causing breakage. The process involves applying pressure to the metal to stretch and compress it along a bend line. This will result in a permanent geometrical change.
Though bends are typically made along a straight line, it is possible to create more complex ones using advanced tools and techniques. In any bending process, the force applied causes the outer metal surface to stretch and increase in length and the inner surface to compress, reducing in length. The length of the material center, known as the inner axis, remains unchanged.
The process uses three main tools, dies, punches, and press brakes. A die serves as the base onto which metal is pressed during bending. This will determine the final angle and shape of the bend.
A punch presses the sheet metal into the die cavity. It applies the necessary force to bend the sheet. The press brake is the machine housing the dies and punches. It is also responsible for generating the force required to bend the material.
Importance of Accurate Sheet Metal Bending Calculations
Accurate sheet metal banding is a central part of any metal fabrication project. Here are some of its practical benefits:
Production Planning
Accurate calculations help the fabricator to anticipate how the material will behave under stress. They inform product quality by making sure that the material meets required the specifications for dimensions and tolerances.
Any miscalculation in this regard can cause the product not to fit into its intended application or assembly. This might cause unwarranted delays.
Minimizing Material Waste
Incorrect calculations often result in improper bends causing materials to go to waste. For projects involving costly materials such as titanium or stainless steel, this can have an adverse effect on final production costs.
Accurate calculations help to optimize material usage for correct bending and cutting the first time. This keeps production costs low and eliminates wastage.
Avoiding Deformation and Defects
Metals often return to their original shape after removing the bending force (springback). Proper calculations account for the factors that can lead to this occurrence (more about springback below). Accurately predicting such behavior, it is possible to avoid the defects that might result.
Production Consistency
In high-volume manufacturing, accurate bending calculations support production workflows. Each part can be consistently produced without trial-and-error processes or the need for manual adjustments. In addition to reducing production time, this increases output and boosts efficiency.
Automating Production Processes
Modern manufacturing uses advanced tools such as CAD (Computer-Aided Design) and CNC (Computer Numerical Control) press brakes. Using this automated system efficiently relies on accurate data input – creating a seamless flow between design and production. In turn, this makes it possible for automated systems to perform with minimal human intervention, reducing the likelihood of errors.
How to Calculate Sheet Metal Bending
Deformation
Deformation refers to how a material changes shape when force is applied to it. In this process, deformation happens when press brakes force the material into a die and cause it to bend.
There are two forms of deformation:
- Elastic Deformation: This is the first phase of deformation where a material stretches or compresses in response to force, but returns to its original shape when the force is removed.
- Plastic Deformation: A material undergoes plastic deformation when force is applied beyond a certain point known as the yield point, permanently changing shape.
Sheet metal bending calculations should account for the transition from elastic to plastic deformation to get an accurate figure and avoid cracks and uneven bends.
Plasticity
Plasticity is the ability of a material to undergo permanent shape change without breaking. For example, different metals have varying plasticity aluminum and brass can bend with ease and are less likely to fracture.
However, low-plasticity materials like titanium or high-carbon steel can easily break during bending and therefore require careful calculations.
Elasticity
Elasticity is the ability of a material to recover its original shape after a bending force is removed. Even after a metal undergoes plastic deformation, there is usually a measure of elastic recovery known as springback.
The level of springback depends on the material type. Highly elastic metals like stainless steel have a higher tendency to spring back and therefore require over-bending. Additionally, tighter bends and thicker materials have less springback, but a larger bend radius can amplify the effect.
Major Factors in Bending Calculations
For accuracy, a fabricator has to account for a number of factors to make sure the material does not lose its structural integrity. These factors include:
Material Properties
The main material properties include metal type, yield strength, and ductility.
- Metal Type
Different metals have distinct properties that determine their behavior during bending. Aluminum is lightweight and highly formable, but can crack if over-stressed.
Stainless steel is strong and has a higher risk of springback. Therefore, it requires more force to bend. Brass and copper are highly ductile and are therefore suitable for intricate bends without the likelihood of cracking.
- Yield Strength
A material’s yield strength determines how much force it can withstand before beginning to deform permanently. Accurate calculations have to account for this to avoid exceeding the material’s limit.
- Ductility
This is a material’s ability to stretch without breaking. Copper and mild steel are highly ductile while some aluminum alloys are brittle.
The K-Factor
The K-factor defines the relationship between a material’s neutral axis and its thickness. It is a ratio that helps a fabricator determine how much the interior surface will compress, and how much the exterior will stretch. This ratio typically ranges between zero and one.
During bending, the axis is the imaginary line that remains unchanged. A K-factor of 0.5 means that the neutral axis falls right in the middle of the material while a higher value indicates that it is closer to the outer surface of the bend.
Note that thinner materials and tighter bends tend to shift the neutral axis closer to the inner surface. On the other hand, a larger bend radius or a thicker material is more likely to keep the neutral axis close to the center of the material.
Bend Allowance, Bend Deduction and Flat Length
These are important calculations that determine the flat length of sheet metal prior to bending. Bend allowance accounts for the material that will be stretched during the bending process.
It is the extra length added to a flat pattern to accommodate the bend. Bend deduction refers to the material that will be removed from the flat pattern to account for compression.
Bend Allowance Formula
Bend Allowance (BA) = (π/180) x R x ϴ + K x T
Where R is the radius of the inner bend surface, ϴ is the bend angle, T is the material thickness, and K is the K-Factor.
Bend Deduction Formula
Bend Deduction (BD) = 2 x ((π/180) x R x ϴ – Bend Allowance
Flat Length Calculation
Flat length is the total length of the material in its unbent state, prior to forming. The importance of this calculation is to cut the right material size before bending. The formula is:
Flat Length (FL) = Straight Length 1 + Straight Length 2 + Bend Allowance (BA)
Straight length 1 refers to the distance between the edge of the material to the start of the bend on one side. Straight length B is a similar distance on the other side.
Tools for Accurate Bending Calculations
Manual Methods
Manual banding calculation methods use standard formulas, calculators, and reference charts and are particularly suited to smaller operations. Reference charts are pre-calculated tables showing bend allowance and deduction values for common materials, angles, and thicknesses. While this method is convenient and cost-effective, it is prone to human error and time-consuming.
Software Tools
CAD software supports digital part design and automatically calculates the bending parameters. They accurately predict final dimensions by simulating the bending process, taking into account the aforementioned factors. Similarly, some CNC press brakes integrate with various software to automate calculation.
These tools simplify the process and are highly accurate even for projects involving complex designs. They are ideal for high-volume operations. They help save time, reduce material wastage, and simplify intricate geometries.
Gauer Metal Products, Inc. – the Perfect Blend of Skills, Expertise, and Experience
Ultimately, the best way to achieve accuracy in sheet metal bending calculations is by combining the right set of tools, expertise, and experience. At Gauer Metal Products, Inc., we bring over 78 years of experience to every project. We guarantee consistency and accuracy in every project.
We leverage the benefits of advanced software and skills for high-quality results that meet even the most demanding specifications and applications. Contact us today to learn how we can help you excel in your next project.