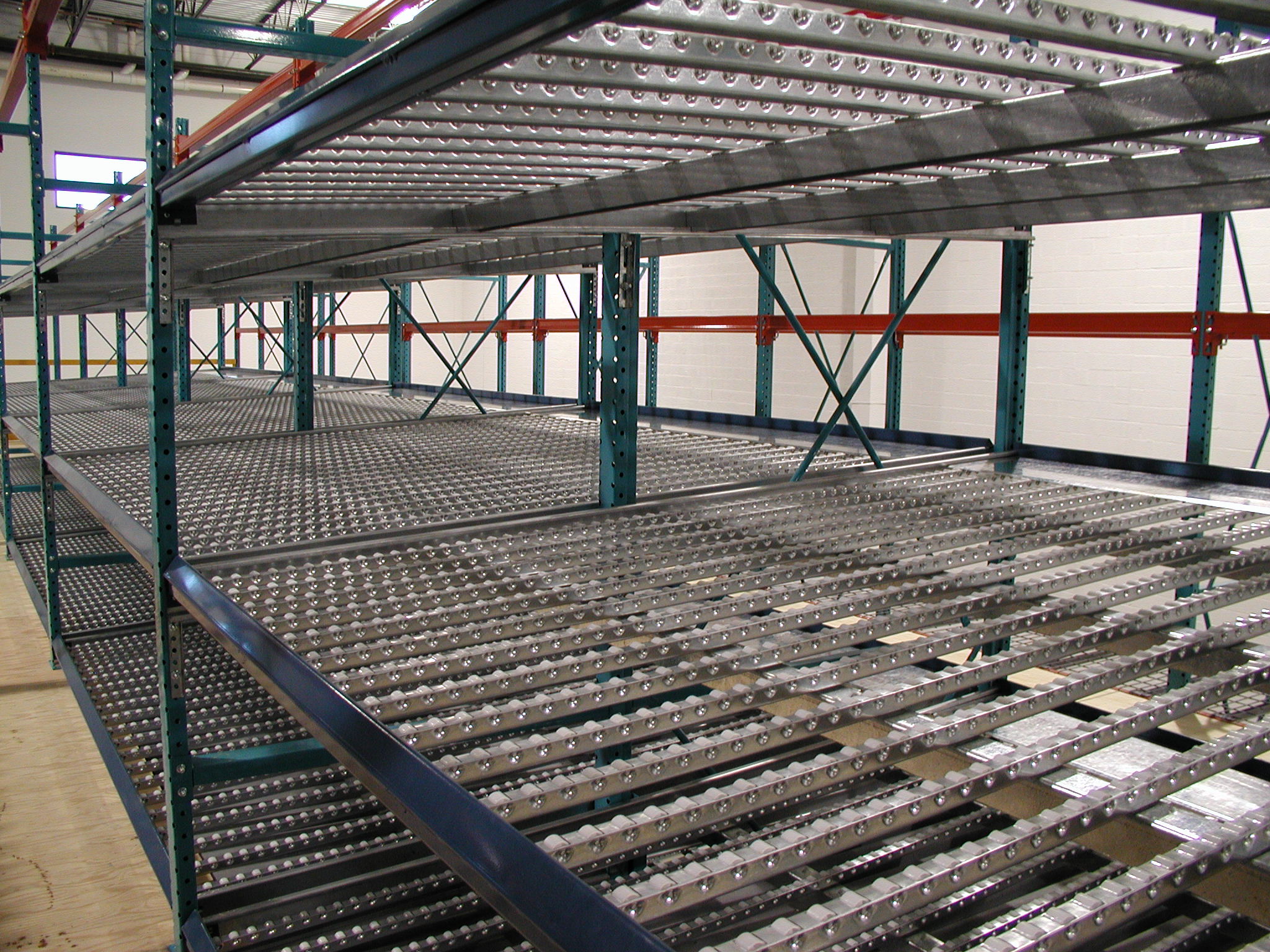
What Are Flow Racks And How Do They Work?
Flow racks, a pivotal component in material handling and storage systems, are designed to optimize efficiency and organization in various environments. They may range from manufacturing plants to large-scale warehouses and retail backrooms, among others. These dynamic storage solutions enable easy access and ergonomic handling of items, facilitating smoother operations and improving workplace safety. In large-scale warehouses, where thousands of levels are common, flow racks are especially advantageous due to their cost-effectiveness and ability to streamline inventory management on a massive scale.
This article explores their structure, functionality, and benefits, providing insights into why they are a favored choice in the warehouse industry
Understanding Flow Racks
These rack systems are also known as gravity flow or dynamic flow systems. As this description implies, they utilize a combination of inclined shelves and gravity rollers to automatically rotate inventory. This system is engineered to adhere to the first-in, first-out (FIFO) inventory management principle.
Based on this feature, they provide an important storage solution in industries where product life span and turnover rate are key concerns.
Some examples of such industries include food manufacturing, cosmetics, electronics, paper products and pharmaceuticals. In all of these industries, items either have an expiration date or tend to degrade over time, requiring an efficient inventory management framework.
Different Types of Flow Rack Systems
There are different types of flow rack systems, each designed to meet specific storage and accessibility needs within various warehousing and manufacturing environments. Here are some of the main types and their components:
- Case Flow or Carton Flow Racks: Designed for hand-loaded items, carton flow racks use gravity rollers or wheels to move boxes or cartons from the back (loading area) to the front (picking area). They are ideal for high-volume order picking and assembly operations.
- Pallet Flow Systems: Similar to carton flow systems but designed for palletized goods. These racks can be equipped with either wheels or rollers and are used in environments where pallets need to be moved efficiently. Pallet flow systems are excellent for storing mass quantities of similar products and expediting the order fulfillment process.
- Gravity Flow Conveyor: This type of conveyor unit uses skate wheels, full-width rollers, staggered wheel rollers, or roller tracks to convey products using gravity. Typically part of a larger system, these conveyors are used primarily to move products, rather than store them, unlike the case flow racks or pallet flow racks mentioned above.
- Case Flow Shelf Systems: Over many decades, the method of using shelf levels to create a case flow or carton flow rack system has been perfected. This is the most versatile way to build such a system. It uses a shelf framework attached to either freestanding uprights or pallet rack posts. The post mount eliminates the need for pallet rack beams to support the level, minimizing lost vertical storage space. These systems can be fitted with roller tracks, low-profile full-width rollers, or low-profile staggered wheel beds.
- Full Width Roller Systems: Popular in the 1990s and early 2000s, this type of carton flow system incorporates roller lanes that can be placed onto existing pallet rack beams. These sections offer a high-density storage option with a smooth flow using either aluminum or steel “cigar” rollers. This system is ideal for items that will not change in size, providing consistent, smooth flow. However, once manufactured, it cannot be modified to accommodate changing product sizes.
- Pick Modules: Multi-level flow systems designed to optimize the order picking process. These modules often combine different types of flow systems and other storage solutions, tailored to the specific needs of a distribution center or warehouse, allowing for efficient movement of goods from storage directly to shipping.
Structure of Flow Systems
A typical gravity flow system is built from a series of sloped storage lanes that allow items to glide down from the loading end to the retrieval end. These lanes are equipped with rollers or wheels, which facilitate the movement of goods. The angle of incline is carefully calibrated to ensure a steady, controlled flow of items, preventing any damage from sudden impacts or excessive speed.
Materials and Construction
These systems are predominantly constructed from durable materials like steel, which ensures longevity and resilience even in high-demand environments. The choice of metal and its thickness are tailored to accommodate the weight and size of stored items, ranging from lightweight components to heavier goods like automotive parts or bulk food items.
How They Work
The functionality of these rack systems is based on the simple yet effective principle of gravity. By harnessing gravity, these racks reduce the need for manual handling, thus decreasing labor costs and enhancing workflow efficiency.
The user loads items into the back of each lane and the items automatically move toward the front as items leave the unloading end. This setup not only keeps inventory well-organized but also ensures that the oldest items are used first, critical for managing expiration dates and reducing waste.
Applications in Various Industries
These systems are versatile and can be adapted to a wide range of industries. In manufacturing, they are used to keep assembly lines supplied with components, ensuring that workers have continuous access without interruptions. Retailers use them in storerooms to manage stock efficiently, keeping shelves replenished and reducing the time spent on restocking.
In distribution centers, they expedite the process of sorting and dispatching products, crucial for maintaining fast operation speeds.
Benefits of Using the Flow System
The adoption of this system brings numerous advantages to any operational setting:
- Increased Efficiency
By automating the movement of inventory, flow racks significantly cut down on the time and effort required to manage stock. This system allows for quick product retrieval and restocking, keeping pace with high-demand environments.
- Space Optimization
They are designed to maximize vertical space, which is often underutilized in storage areas. This design minimizes the footprint of storage systems, freeing up floor space for other uses and improving the overall layout of the facility.
- Improved Ergonomics
These systems reduce the need for workers to bend, stretch, or climb to retrieve items, thereby minimizing the risk of workplace injuries. This ergonomic design fosters a safer and more comfortable working environment, which can also lead to enhanced productivity.
- Better Inventory Management
They simplify inventory management by automatically rotating stock and providing visible access to stored items. This visibility makes it easier to monitor inventory levels and ensures that older stock is used before newer stock, an essential factor in managing perishable goods.
Customization and Maintenance
The ability to customize racks to meet specific operational requirements is one of their greatest strengths. These systems can be designed to accommodate various item sizes, weights, and shapes, ensuring that each setup is perfectly optimized for its intended purpose.
Customization can include adjustable shelves, varying roller types, and modular components that can be easily reconfigured as needs change.
Proper maintenance is crucial for maximizing their lifespan and effectiveness. Regular inspections should focus on the integrity of rollers, the sturdiness of connections, and the absence of any obstructions in the flow lanes. Simple routine checks and timely repairs not only extend the system’s usability but also ensure it operates at peak efficiency.
Choose Gauer Metal Products for Flow Racks
Gauer Metal Products designs, creates and delivers custom metal fabrication solutions in line with your unique demands and business needs. We are experts in the field with over seven decades of experience and we take a collaborative and client-focused approach to every project.
We will work closely with you to understand your operational challenges and design a flow rack system that optimizes your storage and handling processes. Whether you need a standard setup or a complex custom solution, our engineers are skilled in creating systems that improve efficiency and streamline operations.