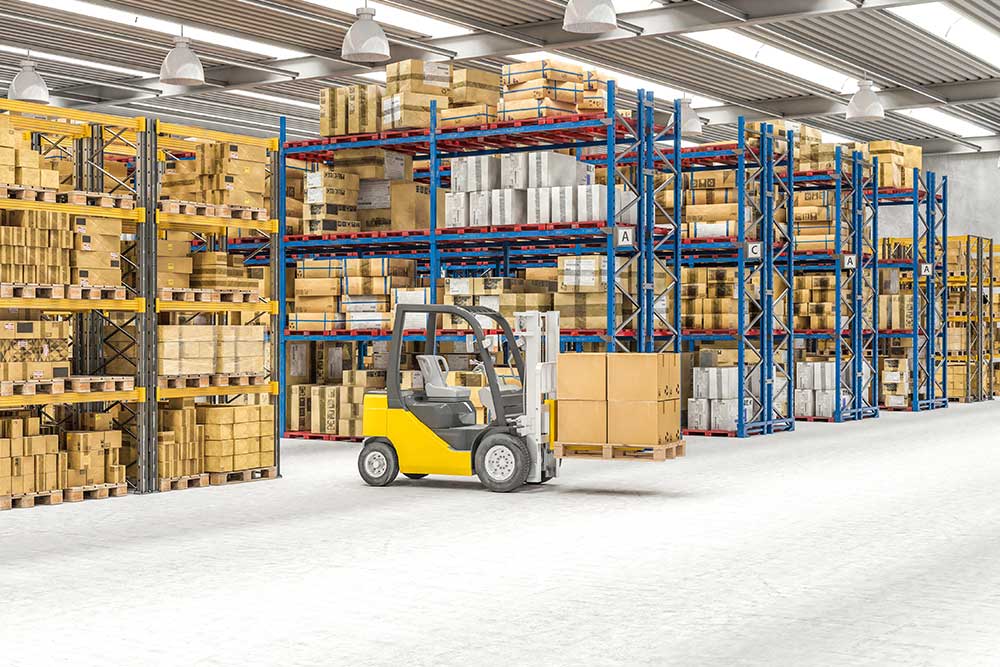
What Are The Types Of Industrial Racking For The Warehouse?
Efficient warehouse management relies on choosing the right industrial racking systems. These systems not only optimize storage space, but also streamline inventory management and improve operational efficiency. At Gauer Metal Products Inc., we specialize in providing high-quality racking solutions designed to meet your various warehouse needs. This article explores the different types of industrial racking for warehouses, so keep reading to learn which type best supports your warehouse operations.
Selective Racking
Selective racking is one of the most widely used and versatile industrial racking systems in warehouses today. It is characterized by its ability to provide direct access to every pallet stored, making it highly efficient for operations where different SKUs or products require frequent picking. This accessibility is facilitated by aisles that separate each rack, allowing forklifts or other handling equipment to maneuver easily between rows.
The key advantage of selective racking is its flexibility. Warehouse managers can easily adjust the storage levels to accommodate varying pallet heights and configurations. This adaptability makes selective racking suitable for warehouses that handle a diverse range of products with different storage requirements. Moreover, because each pallet position is directly accessible, retrieval times are minimized, leading to faster order fulfillment and improved operational efficiency.
Selective racking offers the advantage of accommodating both FIFO (first-in, first-out) and LIFO (last-in, first-out) inventory management systems, making it a versatile choice for warehouses. This flexibility enables warehouses to tailor their inventory rotation strategies according to product shelf life, demand fluctuations, and operational requirements. In scenarios involving perishable goods or items with expiration dates, FIFO ensures that older stock is prioritized for retrieval and shipment, minimizing waste and maintaining the freshness and quality of products throughout their storage lifecycle.
When considering selective racking for your warehouse, it’s essential to evaluate your space utilization needs and operational workflows. By maximizing vertical storage space while maintaining accessibility, selective racking helps warehouses achieve higher storage densities compared to traditional static shelving. This efficiency not only reduces the overall footprint of the warehouse but also enhances inventory visibility and control.
Drive-In Racking
Drive-in racking is designed for warehouses that prioritize maximizing storage capacity over accessibility. Unlike selective racking, which features separate aisles for each rack, drive-in racking utilizes fewer aisles by allowing forklifts to enter the racking structure to retrieve or deposit pallets. This design optimizes floor space utilization by eliminating the need for multiple aisles and dedicating more space to storage.
The primary advantage of drive-in racking is its high storage density. By eliminating aisles and using lanes for forklift access, warehouses can store large quantities of homogeneous products efficiently. Drive-in racking operates on a last-in, first-out (LIFO) inventory management system, where the most recently loaded pallet is the first to be retrieved. This system is particularly suitable for goods that are not time-sensitive and do not require strict inventory rotation.
Additionally, drive-in racking reduces the overall cost per pallet position compared to selective racking systems. With fewer aisles and a higher storage density, warehouses can achieve significant cost savings in terms of both construction and operational expenses. However, it’s important to consider that drive-in racking may not be suitable for warehouses with a high SKU variety or frequent inventory turnover, as it can limit accessibility to individual pallets.
Push-Back Racking
Push-back racking offers a flexible and space-efficient storage solution, perfect for maximizing warehouse capacity while ensuring easy access to stored items. This system operates on a last-in, first-out (LIFO) principle, making it a great choice for facilities that need both high storage density and easy item retrieval. Its design features nested carts that glide on inclined rails within the rack framework. When a new pallet is introduced, it pushes the previously loaded pallets deeper into the lane. This allows for the deep storage of multiple pallets in each lane, enhancing space utilization without sacrificing accessibility.
A key benefit of push-back racking is its improved selectivity compared to traditional drive-in racks. In drive-in systems, you can only access the pallet at the front, but push-back racking provides access to several pallets from the same lane. This selective access simplifies the retrieval of specific pallets, minimizes disruption to other goods, and speeds up picking processes, boosting overall warehouse efficiency.
Push-back racking systems are especially valuable in warehouses managing perishable items or products with different expiration dates. The LIFO approach helps ensure that the most recently added stock sits behind older items, minimizing the risk of spoilage and reducing waste. This is particularly important in industries like food and beverage, pharmaceuticals, and automotive parts, where maintaining product freshness and proper inventory rotation is essential.
Pallet Flow Racking
Pallet flow racking represents an innovative approach to warehouse storage, employing a gravity-fed system to optimize space and streamline inventory operations. This system is tailored for environments handling high-volume and swiftly moving inventory, operating on a first-in, first-out (FIFO) principle. It features inclined shelves outfitted with rollers or wheels, facilitating seamless movement of pallets from loading to picking areas within the rack structure.
The primary advantage of pallet flow racking is its ability to optimize warehouse space by reducing aisle space and maximizing vertical storage capacity. By utilizing gravity to move pallets, this system minimizes the need for forklifts to travel deep into the racks, thereby improving picking efficiency and reducing labor costs. Pallet flow racking is particularly beneficial for warehouses with limited floor space looking to increase storage density without expanding their footprint.
In addition to space optimization, pallet flow racking enhances inventory control and accuracy. The FIFO system ensures that products are picked in the order they were received, reducing the risk of product spoilage and obsolescence. This feature is critical for industries such as retail, distribution, and manufacturing, where efficient inventory turnover is essential for maintaining profitability and customer satisfaction.
Case Flow Racking
Case flow racking, also known as carton flow racking, is a specialized storage system designed for warehouses that handle small to medium-sized items stored in boxes, cases, cartons, or bins. Unlike traditional static shelving, case flow racking utilizes a gravity-fed mechanism to automatically move products from the loading side to the picking side of the rack. This system consists of inclined shelves equipped with rollers or wheels, which facilitate the smooth flow of items based on the principles of first-in, first-out (FIFO) inventory management. Alternatively, case flow can be utilized in a push back system, based on the last-in, first-out (LIFO) inventory management as noted above.
The primary advantage of case flow racking is its ability to enhance picking efficiency and optimize workflow in warehouses with high SKU variability and rapid inventory turnover. By eliminating the need for manual replenishment and reducing travel time within the warehouse, case flow racking accelerates order fulfillment processes and improves overall productivity. This efficiency is particularly beneficial in industries such as e-commerce, retail distribution, and manufacturing, where quick and accurate order processing is essential to meet customer demands.
Moreover, case flow racking supports effective space utilization by maximizing vertical storage capacity and reducing aisle space. The inclined shelves ensure that products are automatically presented at the picking face, minimizing reach and retrieval times for warehouse personnel. This ergonomic design not only increases operational efficiency but also reduces labor costs associated with picking and replenishment tasks.
Cantilever Racking
Cantilever racking is a specialized storage solution designed to efficiently store long and bulky items such as lumber, pipes, tubing, and furniture. Unlike traditional pallet racking systems that utilize horizontal beams and upright frames, cantilever racking features arms that extend from vertical columns. These arms provide uninterrupted storage space along their entire length, allowing for easy loading and unloading of oversized or irregularly shaped items.
The primary advantage of cantilever racking is its flexibility and accessibility. Warehouse operators can adjust the height of the arms to accommodate varying product sizes and shapes, maximizing storage efficiency without wasting vertical space. This adaptability makes cantilever racking ideal for industries such as construction, manufacturing, and retail, where storing and retrieving long or awkwardly shaped items efficiently is essential for maintaining workflow and productivity.
Moreover, cantilever racking enhances safety by providing clear visibility and easy access to stored items. The open design allows forklifts or other handling equipment to maneuver easily within the rack, minimizing the risk of damage to products or injury to personnel. This accessibility also facilitates faster loading and unloading times, reducing handling costs and improving overall operational efficiency.
Automated Storage and Retrieval Systems (AS/RS)
AS/RS systems use automated mechanisms such as cranes and shuttles to store and retrieve items from racks. These systems maximize space utilization and improve picking accuracy and speed, making them ideal for high-volume distribution centers.
Automated Storage and Retrieval Systems (AS/RS) offer numerous advantages by automating repetitive, low-value tasks involved in inventory storage and retrieval. These systems enhance operational efficiency by optimizing floor space usage and reclaiming vertical space, leading to increased storage density. They also improve workplace ergonomics and safety, resulting in fewer accidents and injuries. AS/RS boosts throughput and reduces labor costs, alleviating issues related to labor shortages. The modular design of many AS/RS solutions provides maximum flexibility, allowing for easy adaptation to changing needs. Additionally, these systems enhance order picking accuracy, visibility, and product security, making them a valuable asset for modern operations.
Choosing the right industrial racking system depends on your warehouse layout, inventory characteristics, and operational requirements. Gauer Metal Products Inc. offers a broad range of racking solutions, including advanced case flow racking systems, designed to optimize your warehouse storage space. Contact one of our specialists today and let us help optimize your business operations.