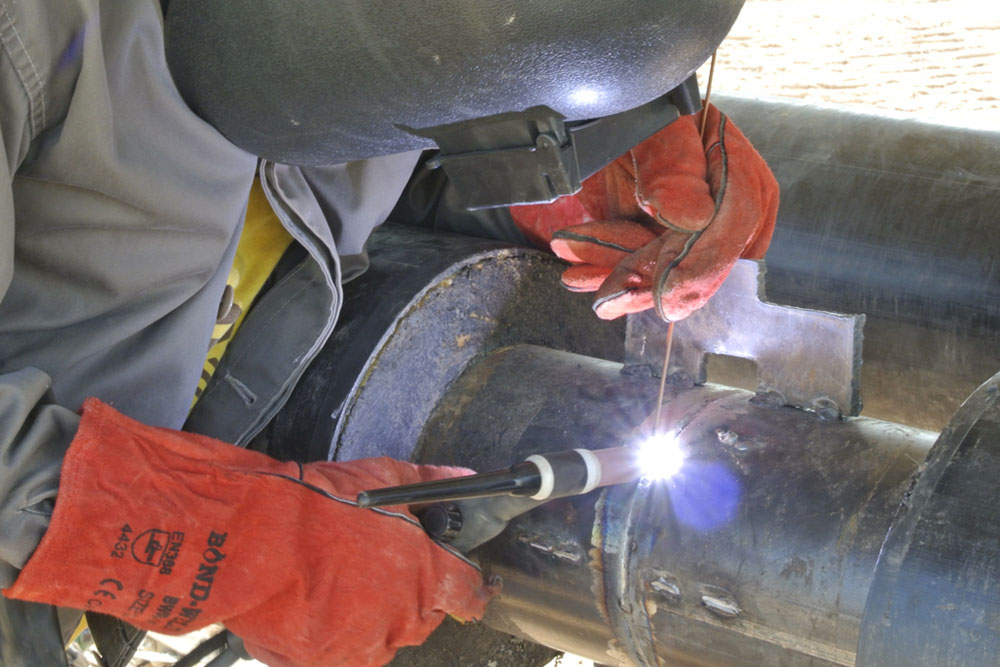
What Gas Is Used In MIG Welding?
Whether you are just starting out in Metal Inert Gas (MIG) welding or are a professional in this technique, you understand the importance of using the right gas. One of the key secrets to achieving a smooth and flawless weld every time revolves around your choice of shielding gas.
What gas is used in MIG welding and why does your choice matter? The answers to these questions depend on the material you are working with and the unique needs of your project. This guide will walk you through the most commonly used gases in MIG welding, their distinctive benefits, and how to choose the best one for your needs.
What is Shielding Gas?
In MIG welding, shielding gas refers to a protective gas that creates a barrier around the molten weld pool, keeping it safe from contamination by moisture and atmospheric gases. While in many cases this is an inert gas (hence the name Metal Inert Gas), some processes use active gases, as well as in greater detail below.
The Role of Shielding Gas in MIG Welding
The MIG welding process involves applying heat to melt a continuous wire electrode in contact with the metal being welded to form a weld pool. As the wire melts, it fuses with the metal to create a joint that solidifies as it cools.
During this process, shielding gas flows around the weld pool to protect it from contamination. This results in a clean weld that is free from oxidation or porosity (holes in the weld). If moisture, oxygen, or carbon dioxide in the atmosphere were to come into contact with the weld pool, it would cause defects that could weaken the weld. Furthermore, it could lead to spattering, which can impact the appearance of the weld negatively.
Shielding gas also plays a role in controlling heat output, because different gases have varying thermal properties. While some gases allow for more intense heat, providing deeper penetration, others slow down heat transfer.
Gauer Metal Products, Inc. has been delivering professional MIG welding services for the past 78 years, and we understand the need to use the right gas for the right project. We use a variety of gases for different types of metals, varying project requirements, and diverse material properties. Here is a more detailed look into the types of gases we use and the factors determining our choice.
Types of Shielding Gases Used in MIG Welding
Inert Gases
The most commonly used inert or chemically non-reactive gases are argon and helium, which are chemically stable and do not react with any external elements. Argon is more affordable than helium, and is, therefore, the more common of the two. However, thick materials requiring a high input of heat sometimes require helium. It brings deeper penetration and faster welding speeds.
Active Gases
Active gases are also described as chemically reactive, in that they can react with elements in the atmosphere during the welding process. When an active gas is used, the process is described as Metal Active Gas (MAG) welding. The only pure active gas used in this welding technique is carbon dioxide (CO2). It is most commonly used in projects that prioritize deep penetration and low cost over the appearance of the weld.
Pure Gases
Pure gas welding involves using a single element in unmixed form for specific welding applications.
Gas Mixtures
Gas mixtures typically combine an inert gas and an active one to achieve desired results by balancing the penetration, arc stability, and spatter control.
Choosing the Right Gas for Different Metals
Aluminum
The most suitable gas to use in the process is 100% Argon. Aluminum is a non-ferrous metal with a low ionization value, meaning it requires a gas that produces excellent arc stability as well as sufficient shielding to prevent oxidation.
Argon creates a smooth and stable arc, controlling heat output and achieving clean welds with minimal spatter. On thin aluminum, it delivers consistent heat, reducing the risk of burn-through. For thick aluminum, most fabricators use a mix of argon and helium to increase penetration.
Steel
Steel welding can use pure CO2, a combination of argon and CO2, or a blend of argon, CO2, and oxygen depending on the desired results and material thickness. CO2 is a semi-inert gas that delivers relatively deep penetration, which is ideal for thicker steel. However, it produces a significant amount of spatter and a rougher finish. The argon-CO2 mix is ideal for thinner material because it does not promote burn-through. It produces less spatter and a clean weld.
For specialized applications where a smooth finish and aesthetics are important, the CO2-oxygen-argon mix is ideal. It requires a small amount of oxygen, typically 1% or 2%, to improve weld pool fluidity, producing smooth and consistent results.
Stainless steel
The most suitable gases for stainless steel welding include pure argon, a mixture of argon and CO2, or a mixture of argon, CO2, and helium. Pure argon is ideal for thin sections of the material or in places where aesthetics are the priority. It creates a smooth arc resulting in a clean weld.
Adding a small amount of CO2 to argon increases penetration and improves fusion without negatively impacting the material’s corrosion resistance. It is suitable for thin to medium-thick materials requiring considerable penetration.
A mixture of argon, CO2, and helium is mostly used for thick materials as it increases the arc heat, promoting deeper penetration. Helium helps in spreading the arc and improving the fluidity of the weld pool, and is particularly beneficial when dealing with high-strength stainless steel.
Copper
Copper requires 100% pure argon, a mixture of argon and helium, or a blend of argon and oxygen as shielding gases, depending on the material thickness and application. Since copper is highly conductive, pure argon works great for thin sections that do not require high heat input. For thicker sections, adding helium to argon increases the heat input for deeper penetration.
Sometimes, fabricators add between 1% and 3% oxygen to wet the copper surface or increase weld pool fluidity. This is ideal for medium-thick sections and it helps to reduce porosity particularly when the surface of copper is not perfectly clean.
Nickel Alloys
Welding this material requires 100% argon, a mixture of argon and helium, or in some cases, a hydrogen-argon blend. Pure argon offers the best results for thin material sections while adding helium increases penetration for thicker sections.
For the argon-helium mix, experts recommend using at least 40% helium because a lower helium content will not bring sufficient heat to significantly improve the weld. Helium has a higher ionization potential than argon, meaning it requires more energy to ionize but in turn, produces higher heat. Using the stipulated helium content increases heat input and delivers deeper penetration.
The mixture of argon and hydrogen is ideal for specific applications where hydrogen acts as a reducing agent, particularly when working with alloys prone to surface contamination. Hydrogen prevents oxidation in such cases but requires careful control as it can lead to porosity.
Other Factors Determining Gas Selection
- Material Thickness: Thin materials require low heat and use pure argon to prevent burn-through, while thick materials call for higher heat input and use helium mixtures to achieve this.
- Desired Welding Speed: Using helium increases the arc temperature and speeds up the welding process, but pure argon is slower and therefore ideal for applications requiring precision.
- Weld Position and Type of Joint: Argon-rich mixtures provide better arc control for complex positions. The presence of CO2 promotes better penetration when dealing with joints that require strong fusion.
- Desired Results: If you are looking for structural integrity and strength, gas mixtures with helium and CO2 are ideal. However, if the goal is to produce a clean, visually appealing weld with minimal spatter, pure argon and argon-CO2 blends work best.
Selecting the Best Gas for Your MIG Welding Needs
Ultimately, your choice of welding gas will depend on the metal you are dealing with, the desired results, and material properties. Take time to learn about these key factors to make the best possible choice and achieve high-quality welds.
Our experts at Gauer Metal Product, Inc. are always on hand to come with professional metal fabrication solutions. We have the skills and experience to provide the best quality MIG, TIG, and spot welding services to suit your unique project requirements. You can always count on us to use the most suitable shielding gases and the best techniques to deliver exceptional outcomes for every project.