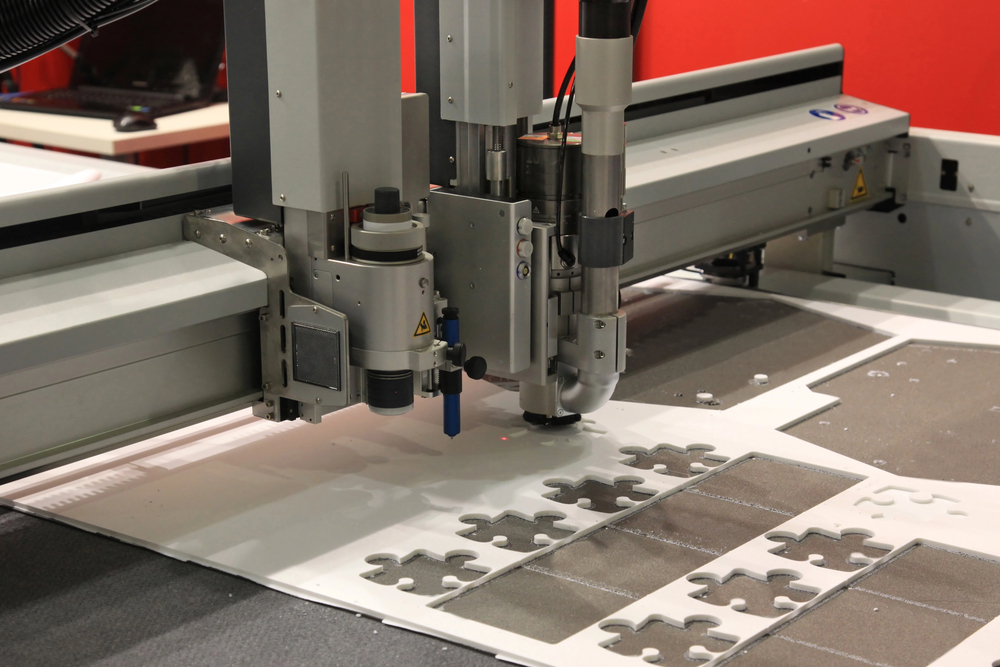
What Is CNC Punching And How Does It Work?
Computer Numerical Control (CNC) punching is a sheet metal fabrication process widely used in industries that require precise and repeatable designs. This method utilizes computer-controlled machinery to punch holes and shapes into metal sheets with unparalleled accuracy. By combining automation and efficiency, CNC punching has significantly improved the manufacturing of components for custom applications and large-scale production alike.
At its core, the process operates on a simple concept: using pre-programmed instructions to control the movement and actions of a punching machine. The machine is equipped with specialized tools capable of cutting, forming, or engraving designs into metal sheets. This process allows manufacturers to meet diverse needs, from intricate decorative patterns to robust structural components.
How CNC Punching Operates
Machines used for the process are powered by software that translates digital designs into physical operations. These machines feature a worktable where the metal sheet is securely positioned. Meanwhile, the punching head moves over it to carry out programmed tasks. The metal sheet may also shift under the punch, depending on the design’s complexity and the machine’s configuration.
The tools used for the process vary depending on the design specifications. A turret-style machine might use multiple tools to perform different punches without interruption. Alternatively, a single-head machine equipped with a tool rail allows for rapid changes between punches. The versatility of these systems makes them an excellent choice for custom metal fabrication, particularly in industries demanding both precision and adaptability.
Materials and Applications
The process is compatible with various materials, including steel, stainless steel, aluminum, and even non-metallic options like wood and plastic. Metal sheets typically range from 0.5mm to 6mm in thickness. This accommodates both lightweight and heavy-duty applications. The adaptability makes the process ideal for creating everything from ventilation panels to brackets and decorative features.
Its applications are diverse, spanning industries such as construction, automotive, electronics, and furniture manufacturing. For example, perforated panels used in architectural projects often rely on this method for their precision and aesthetic appeal. The ability to produce detailed designs and functional components in a single operation significantly enhances productivity.
Advantages of CNC Punching
It offers numerous advantages. Therefore, it’s a preferred choice for many manufacturers. One of the most notable benefits is the accuracy provided by computer-controlled processes. This precision reduces material waste, streamlines production, and lowers costs. Additionally, its automation eliminates much of the manual labor associated with traditional fabrication methods.
Another advantage is the capability to handle complex designs efficiently. Punching machines can produce intricate patterns or repetitive features, such as grids or perforations, without compromising quality. Furthermore, some machines come equipped with features like threading and forming tools, which expand their utility beyond basic punching operations.
Design Considerations for CNC Punching
When planning a project involving this process, it is important to consider certain design aspects to achieve optimal results. Hole size, for instance, should match the thickness of the metal sheet to maintain structural integrity. Similarly, the spacing between holes or shapes affects the overall strength of the finished component.
Advanced techniques, such as using cluster tools, allow manufacturers to punch multiple holes simultaneously. This method is particularly useful for creating patterns like speaker grilles or ventilation slots, saving time while maintaining precision. Engraving tools can also be employed to mark parts with identifiers, such as serial numbers or assembly instructions. They will help enhance the traceability of components.
Why CNC Punching Stands Out
It is a reliable and efficient fabrication method due to its adaptability and precision. Unlike traditional punching methods, which rely heavily on manual labor, CNC systems offer automated solutions that reduce the risk of errors. The ability to reuse digital designs further enhances productivity by eliminating the need to create new templates for recurring projects.
This technology also contributes to sustainability efforts through the reduction of material waste. Because the punching process is highly accurate, leftover material can often be repurposed or recycled. Moreover, the speed when using this process helps manufacturers meet tight deadlines without compromising quality. As a result, it’s an indispensable tool in modern production.
Bringing Precision to Custom Metal Fabrication
CNC punching’s role in custom metal fabrication is particularly noteworthy. It allows manufacturers to produce unique components tailored to specific applications while maintaining a high degree of consistency. From decorative features to functional parts, this process supports innovation across multiple industries. With advanced tools and techniques, it continues to push the boundaries of what is achievable in fabrication.
The impact of the process extends beyond individual components. It plays a critical role in larger systems, where precision and durability are paramount. Whether crafting parts for consumer electronics or industrial machinery, it consistently delivers results that meet stringent requirements.
Modern Innovations in CNC Punching Technology
The evolution of this technology has introduced features that further enhance its versatility and efficiency. Modern machines are equipped with automated tool changers. They allow for seamless transitions between different punching tasks without manual intervention. This will save time and also enable the creation of intricate and multi-functional designs in a single production cycle.
Another innovation is the integration of quality control systems within CNC punching machines. These systems detect material defects or deviations in real-time, halting operations to prevent errors. Such advancements contribute to consistent output. They reinforce the reliability of this process for both high-volume production and bespoke manufacturing projects.
The Role of CNC Punching in Sustainable Manufacturing
It contributes to sustainable manufacturing practices by minimizing waste and optimizing material usage. The precision of this process makes it a point that only the necessary material is removed, reducing scrap and conserving resources. Additionally, many CNC machines are designed to recycle leftover materials, further reducing environmental impact.
The energy efficiency of modern CNC punching equipment also aligns with sustainability goals. These machines operate with lower energy consumption compared to traditional fabrication methods. Thus, they became an eco-friendly choice for manufacturers. Companies can align their production processes with environmental standards while maintaining high levels of productivity by adopting this technique.
High-Quality CNC Punching Results for Different Needs
Gauer Metal Products, Inc. understands the different needs of various industries when it comes to CNC punching services. Our Bottom of Form
High Highpunching and stamping solutions can be used for projects of all sizes, and our team works to meet your fabrication needs with precision and care. Feel free to let us know if you want to learn more.