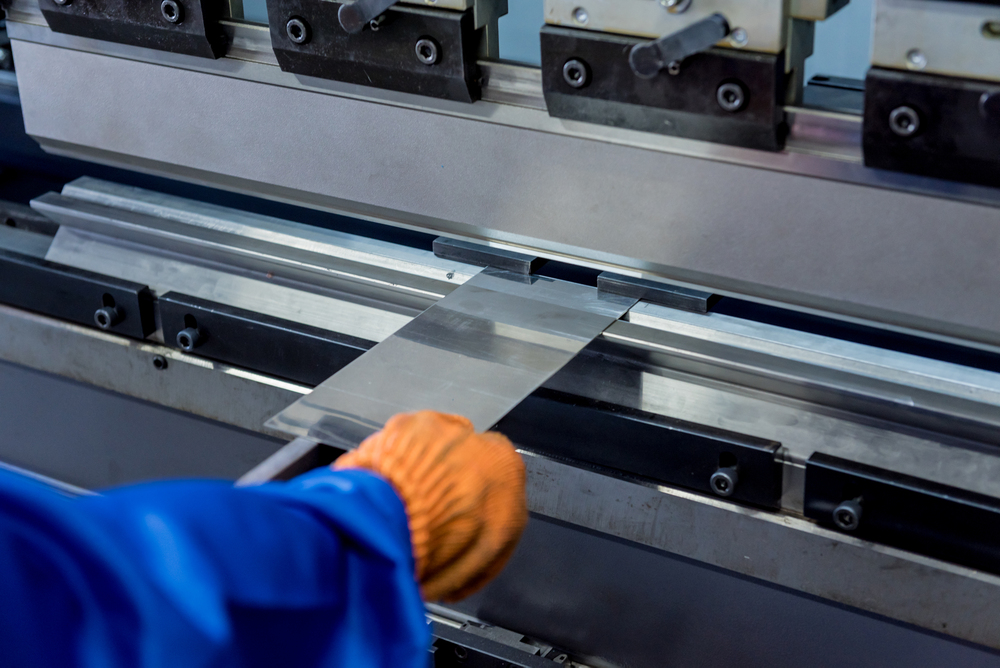
What Is Metal Shearing And How Does It Compare To Other Methods?
There are numerous processing methods used to cut and size metals to precise specifications for various needs. Among these, metal shearing stands out as one of the most common metal cutting methods. However, what is metal shearing and what are its benefits and drawbacks compared to other methods?
In this guide, we will take an in-depth look into this process, understand how it works, and when to use it.
What is Metal Shearing?
Metal shearing is a process used for cutting metal by applying a high force to a material using two sharp blades that push against each other. This high force causes breakage along a desired line.
It works in much the same way as using a pair of scissors to cut through material. Both processes involve two sharp blades moving in opposing directions to create a cutting action along a defined line where the blades meet. However, though the application of pressure in scissors comes from hand force, shearing derives pressure from a shearing machine’s hydraulic or mechanical system.
This process is at times referred to as die cutting. Meanwhile, there are some distinctions between the two. The blades used in shearing are straight and therefore ideal for straight-line cuts. However, die cutting uses custom-shaped dies pressed into a material to cut it into desired shapes.
How Does Metal Shearing Work?
The process typically involves placing metal on a bench and holding it in position. Then, two blades are placed in the shearing machine, a stationary blade at the bottom and a moving blade at the top.
Once the blades are set in place, the next step is adjusting the gap between them to match the material’s thickness. After clamping the material to hold it firmly in place for cutting, hydraulic or mechanical action pushes the upper blade downward with great force to cut through it. Smaller shearing tools use manual action to push the blade down.
For large scale projects, it is possible to stack multiple sheets and shear them simultaneously. Nevertheless, this only works if the machine is capable of handling the combined material thickness. Though this process is generally optimized for straight cuts, some machines can perform angled cuts.
Comparison to Other Metal Cutting Methods
Metal shearing is one of many methods used to cut metals into required sizes and shapes. Here is a brief overview of other methods and how they compare to shearing.
Laser Cutting
Metal laser cutting uses a laser to vaporize materials and create a cut edge. The process typically uses CNC (computer numerical control) and laser optics to guide a laser beam – which melts or burns through the material. This leaves a clean edge and a high-quality finish.
This method is ideal for cutting thin materials and creating patterns. However, it is generally more costly than shearing and tends to be slower.
Plasma Cutting
Plasma cutting uses an ionized gas known as plasma to cut through electrically conductive metals. The ionized gas is heated to an extremely high temperature of more than 20,000 degrees Celsius and ejected under very high pressure. The extreme heat and pressure from the plasma arc melts the material and creates a cut.
The process is highly cost-effective in cutting thick metals and is renowned for high-precision. However, it is not as precise in thinner sheets and can even cause heat distortion.
Waterjet Cutting
Waterjet cutting is a highly efficient cutting process for heat-sensitive materials such as stainless steel and titanium. It uses a stream of water mixed with an abrasive material, ejected at high pressure. The concentrated water jet plus abrasive force physically erodes the metal, cutting through it.
Because this method does not use heat, it does not cause deformation, distortion, or any changes in the properties and structure of the metal. It does not release any harmful gases or vapors, and the water used in the process is recyclable. Nevertheless, it is relatively slow and costly, particularly when used for simple cuts.
Sawing
Sawing uses a toothed band to cut through metal. This is where a blade gradually removes pieces of the material as it moves across the surface. It is great for straight cuts because it created square edges and it can accommodate materials of varying thickness. On the other hand, compared to shearing, it takes more time and is less precise.
Turning
Turning is a lathe machining process that involves rotating a workpiece and gradually shaping it using a cutting tool. A lathe is used to rotate the material while the cutting tool moves along its axis in a linear motion.
As the tool removes metal along the diameter of the workpiece, it gradually creates a cylinder. Depending on the angle of the cutting tool, this process can produce a variety of forms. It is ideally used for round or cylindrical parts.
Oxy-Fuel Cutting
This is a thermal metal-cutting process that heats a metal using a flame consisting of fuel gas and oxygen. It raises the temperature of the metal to the ignition point and then ejects a high-pressure oxygen stream onto the surface. The result is rapid oxidation, which burns away the metal creating a cut.
It is mostly used for thick materials or cuts requiring complex shapes. However, is slower and less precise when compared to shearing.
Is Metal Shearing Better than Other Methods?
Is metal shearing better than other metal-cutting methods? There are a number of unique benefits that make it a more suitable alternative in certain cases:
Key Benefits
Less Waste
One of the main benefits of this method is that it minimizes material waste or kerf. Kerf refers to the width of material removed during cutting or the gap it leaves behind. Kerf width matters in situations requiring accurate dimensions, particularly where tolerances are tight.
Shearing generates minimal to no kerf. This results in virtually no material loss. In comparison, methods such as mechanical sawing, plasma cutting, and laser cutting produce substantial kerf.
Straight Line Cuts
Shearing is highly effective for making straight-line cuts. The material is securely clamped in place. It achieves this with minimal effort and rarely requires adjustments or corrections after the initial cut. While other methods such as laser or plasma cutting are great for cutting shapes, they require more extensive setup and time to cut straight lines.
Clean Cuts
The shearing process uses great force to drive blades through metal sheets. This will bring very clean cuts with smooth edges. Sawing usually leaves jagged edges while plasma and laser cutting can create uneven surfaces due to heat distortion. Using this method therefore removes the need for additional finishing work.
Less Time-Consuming
It is one of the fastest metal-cutting processes because shearing machines are capable of moving through multiple metal sheets in a single pass. This makes it easy to complete high-volume jobs in record time. Comparatively, waterjet and laser cutting, which are ideally used for creating shapes, take significantly longer.
Cost-Effective
The combination of speed and waste reduction makes it one of the most cost-effective cutting methods. It does not require expensive equipment such as waterjet systems and lasers. Additionally, it does not involve the recurring cost of consumables and abrasives.
Moreover, the fact that it reduces the need for finishing work further reduces production costs. This blend of factors places it among the most popular options for high-output operations.
Suitable for Both Soft and Hard Metals
The straightforward mechanical process and customizable setup of this method makes it easy to adjust its use to different material types and thicknesses. Shearing is ideal for working with soft metals such as brass, aluminum, and copper. This is because it avoids melting or burning the material and produces no kerf.
These metals are more malleable and therefore prone to deformation under high heat or abrasive cutting methods. Laser or plasma cutting can overheat or warp them. However, the cold-cutting action of shearing does not affect the material in any way.
For harder metals such as titanium, steel, or stainless steel, the sheer force of this method is sufficient to make clean cuts. To account for the materials’ higher resistance, fabricators use stronger blades and make other adjustments.
Preserves Material Integrity
Sharing maintains the structural integrity of materials because the process uses mechanical force, not heat. The metal remains unchanged and there is no risk of weakening, distortion, or alterations to the temper.
Drawbacks
Like any other method, shearing has its drawbacks particularly when dealing with specific materials. Consider the most significant challenges:
- Potential for Burr Formation: One of the primary drawbacks is the potential for forming burrs along the edges during the cutting process. Burrs refer to small, rough edges or ridges, which may require polishing or deburring to smooth out.
- Cut Quality Depends on Metal Type and Condition: Cutting soft metals is more likely to result in clean, precise edges. Meanwhile, harder or brittle metals might have irregularities along the cut. The material’s thickness and surface condition can also affect the final product.
Get it Right the First Time with Gauer Metal Products, Inc.
While metal shearing has its challenges, its benefits far outweigh any drawbacks. The secret to success lies in managing the process using the right equipment and expertise.
Gauer Metal Products, Inc. has established a solid reputation for offering the most reliable shearing and cutting services across the United States. We have been in business for the past 78 years and our team has a thorough grasp of metal fabrication and related services.
We are experts at what we do. Our team has the skill and advanced equipment for all custom metal fabrication services. No matter what you need, you can count on us to make it happen.
Reach out to us today and let us know how you would like us to solve your production needs.