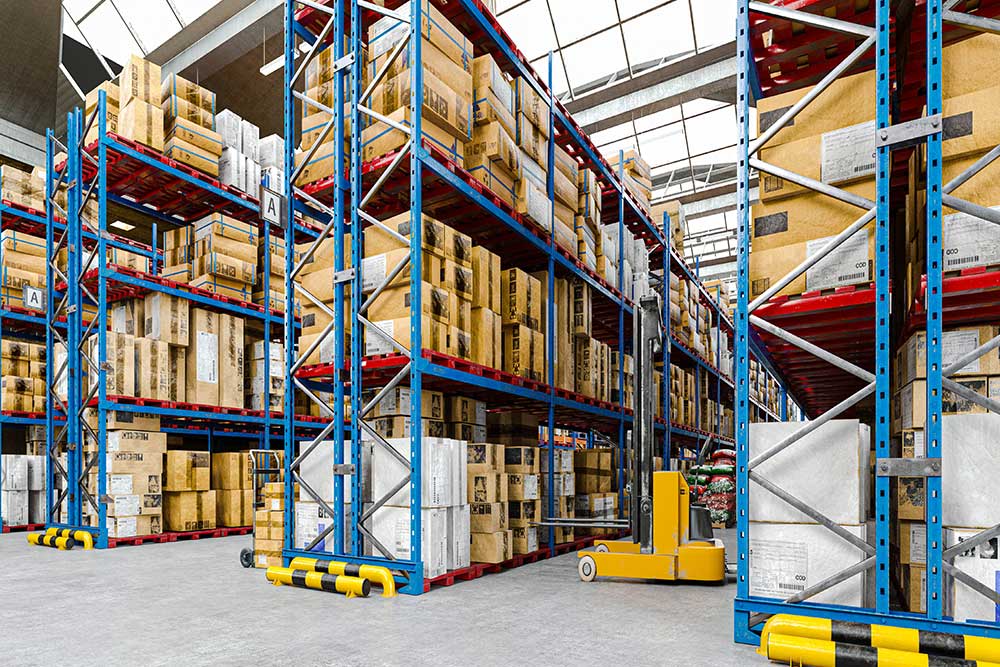
What Is Warehouse Racking And How Does It Benefit Your Business?
Efficient storage solutions are critical for any business involved in logistics, manufacturing, or retail. One of the most effective ways to optimize storage is through warehousing racking systems. At Gauer Metal Products Inc., we specialize in providing top-notch racking solutions that can significantly improve your warehouse operations. Read this comprehensive article to learn more about warehouse racking, its pros and cons, and how these systems can benefit your establishment.
Understanding Warehouse Racking
Warehouse racking is an essential component of modern storage solutions, designed to maximize space utilization and streamline inventory management. As your business grows, so does the need for effective storage solutions that can handle increased inventory without compromising on organization and accessibility. Understanding the various types of racking systems, especially case flow racking, can help you make informed decisions that boost your warehouse efficiency and productivity.
These systems are designed to hold materials in a way that makes them easily accessible while maximizing the use of vertical space. Different types of racking systems cater to various storage needs, and choosing the right one depends on your specific requirements.
Types of Racking Systems
Warehousing racking systems come in a variety of configurations, each designed to address specific storage needs and challenges. Understanding the distinct types can help you choose the most effective system for your operations. Here are some of the main racking systems:
- Selective Racking: This is the most common type of racking system, offering direct access to each pallet. It is highly versatile and suitable for warehouses that store a wide variety of products. Selective racking can be easily adjusted to accommodate different pallet heights and is compatible with various handling equipment, making it ideal for businesses with diverse inventory.
- Drive-In/Drive-Through Racking: This system is designed for high-density storage, allowing forklifts to drive directly into the racking structure to deposit or retrieve pallets. Drive-in racking operates on a last-in, first-out (LIFO) basis, making it suitable for non-perishable or homogeneous products. Drive-through racking, on the other hand, supports a first-in, first-out (FIFO) system, ideal for perishable goods.
- Push-Back Racking: Push-back racking is a dynamic storage solution designed for high-density environments. It features a series of nested carts that glide along inclined rails. When you load a new pallet onto the system, it pushes the previously stored pallets back. Operating on a last-in, first-out (LIFO) basis, push-back racking is ideal for products that do not need strict FIFO inventory management. This system provides improved selectivity compared to drive-in racking while still optimizing the use of available space.
- Pallet Flow Racking: Similar to case flow racking but designed for palletized goods, this system uses gravity rollers to move pallets from the loading end to the picking end. It supports FIFO inventory management and is suitable for high-volume, fast-moving products. Pallet flow racking enhances efficiency by reducing the need for forklifts to travel long distances within the warehouse.
- Case Flow Racking: Also known as carton flow racking, this system is designed for small to medium-sized items stored in cartons. Using sloped shelves and gravity rollers, products automatically move to the front of the rack for easy picking. Case flow racking is ideal for high-turnover inventory, ensuring that items are always accessible and reducing picking times significantly.
Each racking system has its unique benefits and is suited to different warehouse operations. Careful consideration of your storage needs, product types, and warehouse layout will help you select the most appropriate racking solution, thereby enhancing your overall efficiency and productivity.
What Is Case Flow Racking?
Case flow racking, also known as carton flow racking or just simply flow rack, stands out as a dynamic and exceptionally efficient storage solution tailored for small to medium-sized items stored in boxes, cases, cartons or bins. In contrast to traditional static shelving, case flow racking operates on a gravity-fed mechanism. Products are loaded onto the higher end of the rack and effortlessly flow down to the picking end. This system features inclined shelves equipped with rollers or wheels, facilitating seamless movement of items from loading to picking locations.
The primary advantage of case flow racking is its ability to facilitate first-in, first-out (FIFO) inventory management. This is particularly beneficial for businesses that deal with perishable goods or products with expiration dates that can range from pharmaceuticals to food and beverage items and cosmetics. By ensuring that older items are picked first, case flow racking helps maintain product freshness and reduces waste.
Case flow racking systems are also highly customizable and can be adapted to fit various warehouse configurations and product types. The racks can be adjusted to accommodate different carton sizes, weights, and volumes, making them versatile for a wide range of applications. Additionally, the system can be integrated with other warehouse equipment, such as conveyors and automated picking systems, to further enhance efficiency and streamline operations.
One of the key benefits of case flow racking is the significant reduction in labor costs. Since items are always at the front of the shelf and readily accessible, pickers spend less time searching for products, leading to faster order fulfillment and increased productivity. This system also minimizes the need for forklifts or other heavy machinery to move items around the warehouse, reducing the risk of accidents and damage to products.
Benefits of Case Flow Racking
Case flow racking offers a multitude of benefits that can significantly enhance the efficiency and productivity of your warehouse operations. One of the primary advantages is the improvement in picking efficiency. Since the items automatically flow to the front of the rack, pickers can quickly access the products they need without having to search through the shelves.
Another major benefit is the optimization of space utilization. Case flow racking maximizes the use of vertical space, allowing you to store more items in a smaller footprint. This is particularly important for warehouses with limited floor space, as it enables you to increase your storage capacity without the need for additional square footage. By reducing the overall footprint of your storage area, you can also free up valuable space for other operations, such as packing and shipping.
Case flow racking also supports effective inventory management through its first-in, first-out (FIFO) system. This is especially beneficial for businesses that handle perishable goods or products with expiration dates, as it ensures that older items are picked first, reducing the risk of spoilage and waste. Maintaining a consistent inventory rotation can also help improve stock accuracy and reduce the likelihood of overstocking or stockouts.
In addition to these operational benefits, case flow racking can also lead to significant cost savings. By reducing the time and labor required for picking and replenishment, you can lower your labor costs and improve overall productivity. The system’s design minimizes the need for forklifts or other heavy machinery, which can further reduce operational expenses and the risk of product damage or workplace accidents.
Moreover, case flow racking systems are highly durable and require minimal maintenance, offering long-term savings on repair and replacement costs. Investing in a high-quality case flow racking system can provide a substantial return on investment by enhancing your warehouse efficiency, optimizing space utilization, and reducing operational costs. These benefits collectively contribute to a smoother, more efficient, and cost-effective warehousing operation.
How Case Flow Racking Works
The mechanics of case flow racking are straightforward yet remarkably effective, making it a popular choice for warehouses aiming to enhance their operational efficiency. The system relies on gravity to move products from the loading end to the picking end. When items are placed on the higher end of the rack, they naturally move down the inclined shelves toward the picking side due to the force of gravity. This continuous flow ensures that products are always accessible at the front of the shelf, ready for immediate picking.
At the core of the case flow racking system are the sloped shelves equipped with rollers or wheels. These components are designed to facilitate smooth and consistent movement of products. The shelves are typically set at a slight angle to allow gravity to do the work, eliminating the need for manual pushing or pulling of items. The rollers or wheels ensure that even heavy cartons can move effortlessly from the loading zone to the picking zone.
Case flow racking systems are highly adaptable and can be customized to fit the specific needs of your warehouse. The racks can be adjusted to accommodate various carton sizes, weights, and volumes, making them suitable for a wide range of products. Additionally, the system can be integrated with other warehouse equipment, such as conveyors and automated picking systems, to further streamline the picking process and enhance overall efficiency.
Loading products onto the case flow racking system is straightforward. Workers place items at the higher end of the rack, where they are guided by the inclined shelves and rollers to move down to the picking end. This setup ensures that the oldest items are always at the front, supporting effective FIFO inventory management. This is particularly important for businesses dealing with perishable goods, as it helps maintain product freshness and reduce waste.
Choosing the Right Racking System
Selecting the right racking system for your warehouse is crucial to optimizing storage efficiency and meeting your specific operational needs. It involves a thorough evaluation of various factors, including the types of products you store, the frequency of inventory turnover, available warehouse space, and your budget. For businesses with a high volume of small to medium-sized items that require quick access, case flow racking is an excellent choice.
This system supports efficient FIFO inventory management and ensures that products are always accessible for picking. Consulting with a racking specialist can help you assess your needs and determine the best racking solution. They can provide insights on the most suitable configurations and assist with the planning and design to maximize space utilization and operational efficiency. Investing in the right racking system can lead to significant improvements in productivity, inventory accuracy, and overall warehouse performance.
Installation and Maintenance
Proper installation and maintenance are key to the longevity and performance of your racking system. Ensure that your case flow racking is installed by professionals who can tailor the setup to your specific needs. Regular maintenance checks will help prevent wear and tear, ensuring the system operates smoothly and safely over time.
Partnering with Gauer Metal Products Inc.
Gauer Metal Products Inc. offers a range of high-quality warehousing racking solutions, including state-of-the-art case flow racking systems. Our products are designed to meet the diverse needs of businesses across various industries, supporting proper organization and efficient operations. Contact us today for help on streamlining your warehouse operations!